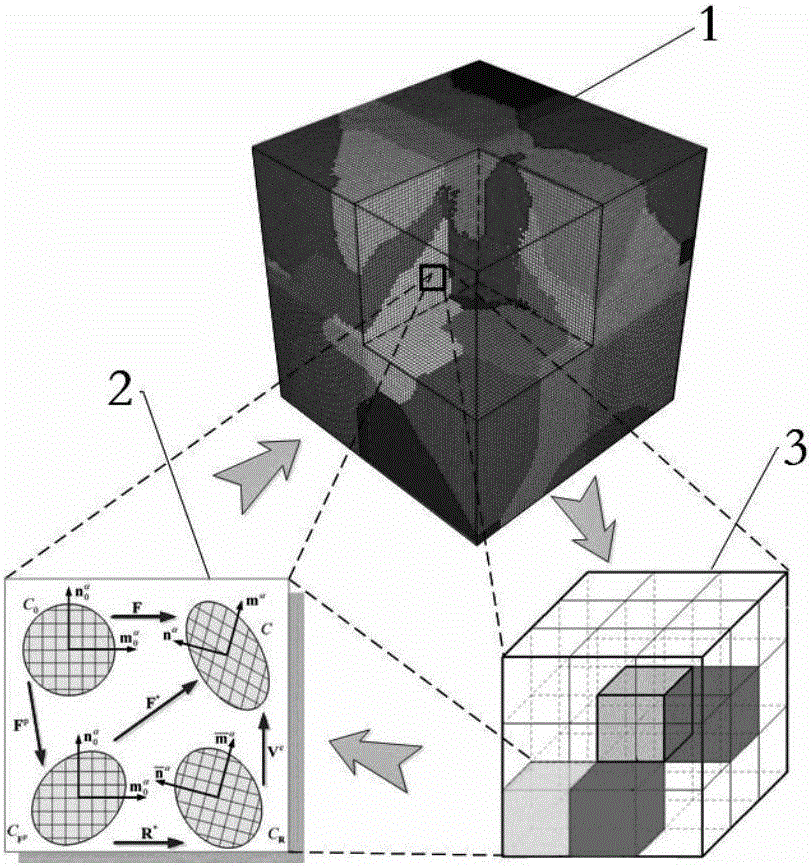
本發(fā)明涉及塑性加工領域,具體是一種預測鈦合金等溫成形與動態(tài)再結晶演化耦合響應的方法
背景技術:
:等溫成形技術是實現(xiàn)鈦合金復雜構件成形成性一體化精確制造的有效途徑。然而,鈦合金等溫成形是一個多參數(shù)、多場耦合作用下的不均勻變形過程,強烈的不均勻變形使得鈦合金等溫成形過程中動態(tài)再結晶形核與長大規(guī)律十分復雜,而動態(tài)再結晶又顯著地影響鈦合金的力學響應,進而對后續(xù)變形產(chǎn)生顯著影響,加劇變形的不均勻性。等溫成形與動態(tài)再結晶演化的耦合作用使得鈦合金變形與微觀組織的預測進而實施控制面臨巨大挑戰(zhàn)。因此,發(fā)展鈦合金等溫成形與動態(tài)再結晶耦合響應的精確預測方法,對發(fā)展鈦合金等溫成形與組織演化全耦合預測理論與方法,進而實現(xiàn)鈦合金構件等溫成形和組織性能的有效控制的具有重要的理論意義和工業(yè)應用價值。在ZL200910012127.4的發(fā)明中公布了采用元胞自動機法對板帶鋼再結晶組織演變進行預測的方法,獲得了板帶鋼高溫變形過程中的動態(tài)再結晶形核與長大及組織形態(tài)演化規(guī)律,并基于平均位錯密度結合Kocks-Mecking(K-M)方程計算了材料的應力響應。但是,這些元胞自動機模型是以晶粒均勻變形為前提條件,未考慮實際成形過程中晶粒尺度的不均勻變形的作用;同時,基于平均位錯密度計算的材料的應力響應不能反映材料實際成形過程中位錯的不均勻分布對應力響應的影響;另外,沒有考慮動態(tài)再結晶組織演化及材料力學響應變化對后續(xù)高溫變形過程的影響。從而使得預測結果的可靠性差。針對這些存在的問題,西北工業(yè)大學的武川等(WuChuan,YangHe,LiHongWei.Modelingofdiscontinuousdynamicrecrystallizationofanear-atitaniumalloyIMI834duringisothermalhotcompressionbycombiningacellularautomatonmodelwithacrystalplasticityfiniteelementmethod.ComputationalMaterialsScience.2013,79:944~959.)將晶體塑性有限元與元胞自動機通過網(wǎng)格映射和變形信息單向傳遞的方法結合起來,以描述晶粒尺度不均勻變形對動態(tài)再結晶形核與長大的影響,并應用于鈦合金等溫成形的不連續(xù)動態(tài)再結晶預測,獲得了鈦合金等溫成形的晶粒變形形態(tài)和動態(tài)再結晶動力學規(guī)律。但該模型依然采用平均位錯計算材料的應力響應,且該模型中晶體塑性有限元與元胞自動機采用相互獨立的網(wǎng)格模型和坐標系,且兩者的網(wǎng)格密度不一致,這使得數(shù)據(jù)傳遞比較困難,且最主要的是僅實現(xiàn)了單向傳遞,導致材料變形與動態(tài)再結晶演化被割裂成兩個系統(tǒng),仍然沒有考慮動態(tài)再結晶對材料后續(xù)變形的影響。加拿大學者Popova等(E.Popova,Y.Staraselski,A.Brahme,R.K.Mishra,K.Inal.Coupledcrystalplasticity-probabilisticcellularautomataapproachtomodeldynamicrecrystallizationinmagnesiumalloys.InternationalJournalofPlasticity.2014,66:85~102)在武川模型的基礎上,通過采用相同網(wǎng)格模型,改善了武川模型中數(shù)據(jù)單向傳遞的精度,但沒有從根本解決上述問題。另外,上述工作均采用二維元胞自動機模型,難以描述實際材料的真實微觀特征,如三岔晶界、四岔晶界等,顯著的制約和限制了材料成形與動態(tài)再結晶規(guī)律的預測精度。技術實現(xiàn)要素:為克服現(xiàn)有技術中存在的未考慮組織演化對后續(xù)變形影響的不足,本發(fā)明提出了一種預測鈦合金等溫成形與動態(tài)再結晶演化耦合響應的方法本發(fā)明的具體實施步驟是:步驟1,生成α+β兩相鈦合金等軸晶初始組織:所述兩相鈦合金等軸晶初始組織中,α相體積分數(shù)為22%,晶粒總數(shù)為40的等軸晶初始組織。步驟2,建立包含晶粒和晶界的鈦合金等溫成形三維有限元模型:將步驟1生成的α+β兩相鈦合金等軸晶初始組織信息導入ABAQUS軟件,生成包含α+β兩相鈦合金等軸晶組織的變形體。采用立方體單元對所述變形體劃分網(wǎng)格,從而建立有限元幾何模型。得到的限元幾何模型為晶體塑性有限元方法和元胞自動機共用,即每個有限元單元也就是一個元胞。對該有限元幾何模型中的α相單元和β相單元分別賦予材料參數(shù)。該有限元幾何模型采用周期性邊界條件,加載方式為單軸壓縮。從而建立了包含晶粒和晶界的鈦合金等溫成形三維有限元模型。步驟3,讀取相關數(shù)據(jù):讀取各有限單元上一增量步的變形梯度、拉伸張量U*和晶?;葡滴诲e密度ρa、晶粒半徑、晶粒取向Q、相信息參數(shù)Ph、晶界參數(shù)Bdy、格林應變的共軛應力T*、滑移系a上滑移方向矢量ma、滑移系a上滑移面單位矢量na以及當前增量步的變形梯度。所述晶粒滑移系位錯密度ρa的初始位錯密度取109m-2;所述滑移系滑移方向ma、滑移面矢量na均位于晶體軸坐標系中。若讀取的相信息參數(shù)Ph為1則采用α相參數(shù)進行后續(xù)步驟的計算;若為讀取的相信息參數(shù)Ph為0則采用β相參數(shù)進行后續(xù)步驟的計算。若讀取的晶界參數(shù)Bdy為0表示非晶界元胞,若讀取的晶界參數(shù)Bdy為1表示晶界元胞。步驟4,確定晶粒間不均勻變形、單元的應力響應和晶粒取向演化:所述不均勻變形指應變在晶粒間和晶粒內(nèi)的不均勻分布。確定晶粒間不均勻變形、單元的應力響應和晶粒取向演化的具體過程是:第一步、通過分解剪應力τa和滑移系抗力sa確定剪切應變速率其中,γ0為參考剪切應變速率,χ為率敏感因子。第二步、計算變形梯度的塑性部分、非塑性部分和格林應變。第三步、通過彈性本構關系計算單元的柯西應力。第四步、計算晶粒取向的轉(zhuǎn)動。至此,確定了晶粒間的不均勻變形、應力響應和晶粒取向演化。所述計算分解剪應力τa和滑移系抗力sa的具體過程是:第一步、根據(jù)公式確定滑移系分解剪應力τa,其中T*為格林應變的共軛應力,其中:為Schmid張量,τa是滑移系分解剪應力。第二步、根據(jù)位錯密度計算滑移系抗力sa其中,s0為初始滑移抗力,sd為位錯交互作用對滑移抗力的影響,sHP為霍爾佩奇效應對滑移抗力的影響,λ為晶界軟化因子。初始滑移抗力表示為變形溫度的函數(shù):其中,c3為與固溶強化相關的強度系數(shù),c6為與材料相關的參考溫度,θ為單元溫度。位錯交互作用對滑移抗力的影響sd為:其中,c4為材料常數(shù),其值在0.1~1之間;b是泊氏矢量;t-△t指上一增量步,相應的t則指的是當前增量步;μ為剪切彈性模量,與溫度有關,通過公式(4)確定:霍爾佩奇效應sHP代表的晶粒尺寸對變形的阻礙作用表示為:其中,c5為霍爾佩奇系數(shù),r為晶粒半徑。鈦合金晶界在高溫變形中的作用如圖3所示,通過公式(6)計算軟化因子:其中,θmelt為材料熔點;為等效塑性應變;為宏觀應變速率。步驟5,計算晶粒的位錯密度演化;根據(jù)晶粒的滑移剪切應變速率計算晶粒的位錯密度演化。同時考慮動態(tài)再結晶與變形中的動態(tài)回復,通過公式(17)計算位錯密度:其中,ki為由于再結晶軟化產(chǎn)生的位錯密度修正系數(shù),ρa+為可動位錯不動化造成的位錯密度增加,即加工硬化效應。ρa-為位錯攀移、異號位錯相消造成的位錯泯滅。ρa+和ρa-分別通過公式(18)和(19)計算:其中,(18)和(19)式中林位錯與不動位錯密度存在如下關系:其中,N為滑移系總數(shù);m與n分別為位錯滑移方向與滑移面法向方向;為滑移系b的不動位錯密度。步驟6,模擬動態(tài)再結晶演化。將晶粒位錯密度作為變量傳遞給元胞自動機,計算動態(tài)再結晶演化。具體過程是:第一步、確定元胞狀態(tài)變量:所述元胞狀態(tài)變量包括:位錯密度狀態(tài)變量:每個元胞的位錯密度為以及滑移系位錯密度為相狀態(tài)變量Ph:用于標定元胞的相信息,Ph=1為α相,Ph=0為β相;再結晶狀態(tài)變量Drx:用于標定元胞是否為新生成的再結晶相,Drx=1表示該元胞為再結晶相,Drx=0表示該元胞為母相;再結晶潛在形核狀態(tài)變量Potential:若母相元胞未轉(zhuǎn)換為再結晶潛在形核元胞,則Potential=0;否則,Potential=1;晶界狀態(tài)變量Bdy:用于標定元胞是否在晶界處,若讀取的晶界參數(shù)Bdy為0表示非晶界元胞,若讀取的晶界參數(shù)Bdy為1表示晶界元胞。晶粒取向狀態(tài)變量Q:描述晶粒取向的張量;晶粒尺寸狀態(tài)變量r:該晶粒的平均晶粒半徑;晶粒編號狀態(tài)變量Grain:包含母相晶粒與新生成的再結晶晶粒,每個晶粒都有不同的編號,處于同一個晶粒的元胞編號相同,處于不同晶粒的元胞編號不同。第二步、根據(jù)形核規(guī)則判斷是否形核;當變形基體內(nèi)位錯密度與臨界位錯密度滿足關系式ρi≥ρc時,新的無應變的晶核將以形核率在變形嚴重的區(qū)域形核,則該元胞轉(zhuǎn)換為t時刻潛在形核元胞,即有:其中,Qint為界面能;l為位錯自由程;Qline為位錯線能量;M為晶界遷移率,M為:其中,δD0b為特征晶界厚度與絕對0度晶界自擴散系數(shù)之積;KB波爾茲曼常數(shù);Qdiffu自擴散激活能;R為氣體常數(shù);b為柏氏矢量。通過公式(23)計算位錯線能量Qline:形核率由公式(24)計算:其中,CN為擬合參數(shù),m為再結晶形核率指數(shù),Qact為形核激活能,θ為溫度。為保證在變形嚴重區(qū)域優(yōu)先形核,根據(jù)每個元胞的位錯密度值,引入形核概率Pnuclei(i)來描述潛在形核元胞i轉(zhuǎn)變?yōu)樵俳Y晶晶核的概率,Pnuclei(i)計算為:其中,ρ(i)為t時刻潛在形核元胞i的位錯密度,ρmax為t時刻潛在再結晶形核元胞中最大位錯密度。隨機選取N(t)個t時刻潛在再結晶形核元胞并生成隨機數(shù)ξ,如果ξ≤Pnuclei(i),則該元胞轉(zhuǎn)換為再結晶晶核元胞,即有:第三步、再結晶長大;一旦元胞開始形核,就會以速率v向其臨近元胞長大,考慮單獨形核和集中形核兩種情況,對每一個母相元胞,計算其被相鄰再結晶元胞吞噬的概率:若中心母相元胞i只有一個再結晶元胞鄰居j,長大距離si,j通過公式(27):其中,t1為上一次si,j置零的時間,晶界遷移的速度v為:vi,j=MP(28)其中,M為晶界遷移率,P為晶界遷移驅(qū)動力。晶界遷移驅(qū)動力P為:P=Pd-Pr(29)其中,Pd為促進晶界遷移的驅(qū)動力,Pr為阻礙晶界遷移的驅(qū)動力。Pd為:其中,ρM與ρR分別為母相與再結晶相的位錯密度。Pr為:req為晶界等效曲率半徑,Qm大角度晶界能。等效曲率半徑為:其中,Ni為晶粒編號Grain=i的元胞總數(shù)目,Vcell為單個元胞所代表的實際變形組織的體積。大角度晶界能計算為:其中,Om為晶粒取向差,v為泊松比,μ為剪切模量。對于元胞i與元胞j,晶粒取向差可以計算為:其中,Qi與Qj分別為元胞i與元胞j的晶粒取向矢量矩陣。引入球形膨脹概率因子Pi,j來描述中心元胞被再結晶鄰居吞噬轉(zhuǎn)換為再結晶元胞的概率,Pi,j計算為:其中,r0為參考半徑,0.98、0.57與0.17分別表示為以中心元胞的為球心,以1.5r0為半徑的球體被鄰居元胞切割的體積與單位元胞的體積的比值。如果si,j≥l,則生成隨機變量ζ∈[0,1]。若ζ≤Pi,j,則中心元胞i轉(zhuǎn)換為再結晶元胞,長大距離狀態(tài)變量si,j置零,中心母相元胞i的位錯密度狀態(tài)變量、相狀態(tài)變量、再結晶狀態(tài)變量、晶粒取向狀態(tài)變量以及晶粒編號狀態(tài)變量均與相鄰再結晶元胞j的狀態(tài)變量相等。如果中心元胞有多個再結晶鄰居,對每個再結晶鄰居進行判斷,若中心元胞滿足能夠同時被多個鄰居吞噬的條件,則優(yōu)先被具有較大Pi,j的再結晶元胞吞噬。具體規(guī)則如下所示:若中心元胞具有n個再結晶元胞鄰居,則記錄該中心的所有再結晶元胞鄰居{j1,j2,......,jn}。計算中心元胞i對所有再結晶元胞鄰居{j1,j2,......,jn}的生長概率{Pgrowth(1),Pgrowth(2),......,Pgrowth(n)}。從再結晶元胞鄰居{j1,j2,......,jn}選取最大Pgrowth對應的鄰居元胞jx,計算長大距離si,j,且生成隨機變量ζ∈[0,1]。若si,j>l且ζ≤Pi,j,則中心元胞被元胞jx吞噬。若不滿足條件,則再結晶元胞鄰居集{j1,j2,......,jn}去掉元胞jx元素,生長概率{Pgrowth(1),Pgrowth(2),......,Pgrowth(n)}去掉Pgrowth(x),然后對剩下的n-1個鄰居元胞按上述方法繼續(xù)進行計算。如果si,j<l,則長大距離狀態(tài)變量si,j隨時間t繼續(xù)積累。第四步、晶界的演化;計算每次形核和長大發(fā)生后的晶界演化。其方法為:判斷中心元胞與鄰居元胞的晶粒編號狀態(tài)變量Grain是否相等,即判斷是否滿足:Grain(j)=Grain(i);j∈{元胞i的所有鄰居}(36)若滿足上述條件,則該元胞處于晶粒內(nèi)部,晶界狀態(tài)變量Bdy=0;若不滿足則該元胞處于晶界上,即有晶界狀態(tài)變量Bdy=1。至此,完成動態(tài)再結晶演化的模擬。步驟7,更新晶粒的位錯密度;根據(jù)模擬得到的動態(tài)再結晶演化更新晶粒的位錯密度。步驟8,確定位錯密度修正系數(shù);步驟9,確定再結晶體積分數(shù);式中,Xnew為新生成的再結晶晶粒,即Drx=1的元胞所占元胞數(shù)目,X為元胞空間總元胞數(shù)目。步驟10,確定當前增量步變形體的流變應力σ;通過公式(41)計算流變應力并輸出:其中Ti為每一個有限元單元的應力響應,NG為晶粒數(shù)目;步驟11,存儲公共變量;將更新后的相信息Ph、晶界參數(shù)Bdy、位錯密度ρi、晶粒尺寸req、再結晶體積分數(shù)f作為公共變量存儲,以便于下一增量步采用晶體塑性有限元法計算下一時刻的不均勻變形;步驟12,當前時刻晶體塑性有限元與元胞自動機的一次耦合。輸出動態(tài)再結晶的組織形態(tài)、再結晶晶粒尺寸、流變應力曲線、再結晶體積分數(shù)及其隨變形的演化;至此,完成了當前時刻晶體塑性有限元與元胞自動機的一次耦合。步驟13,返回有限元模型,重復步驟3~12,進行下一增量步的計算,直至完成鈦合金等溫成形與動態(tài)再結晶演化耦合響應的預測。本發(fā)明的特征在于:采用晶粒長大的3D元胞自動機算法生成鈦合金三維微觀組織模型1,基于ABAQUS/Explicit軟件平臺建立該鈦合金組織模型的有限元網(wǎng)格,同時作為晶體塑性有限元計算變形的網(wǎng)格模型和元胞自動機計算動態(tài)再結晶的元胞模型。然后,采用晶體塑性有限元方法計算鈦合金等溫成形過程中晶粒的應力響應、晶粒間不均勻變形及其導致的不均勻位錯密度分布,并將晶粒的位錯密度等作為變量傳遞給元胞自動機,計算在該晶粒尺度不均勻變形條件下的動態(tài)再結晶演化,獲得動態(tài)再結晶形核、長大的組織形態(tài)及其導致的晶界演化和更新的位錯密度,然后將元胞機計算獲得的動態(tài)再結晶形核及長大等晶粒與晶界信息及位錯密度返回晶體塑性有限元方法,更新每個晶粒單元的位錯滑移抗力,從而影響鈦合金的后續(xù)變形,并通過本構關系計算晶粒尺度的應力響應。從而反映鈦合金等溫成形與動態(tài)再結晶演化的耦合作用。本發(fā)明基于三維鈦合金微觀組織的有限元網(wǎng)格模型,將3D元胞自動機算法完全耦合進晶體塑性本構模型,統(tǒng)一采用材料變形的物理時間,從而實現(xiàn)鈦合金等溫成形與動態(tài)再結晶演化耦合響應的同步預測,為研究揭示鈦合金大型復雜構件等溫成形與組織演化規(guī)律,并進而實施有效控制提供依據(jù)。故而,本發(fā)明能夠獲得鈦合金等溫成形過程中晶粒的不均勻變形分布、不均勻位錯密度分布、不均勻動態(tài)再結晶形核和長大及其導致的組織形態(tài)演化、動態(tài)再結晶導致的應力軟化和應力軟化對后續(xù)不均勻變形的作用,從而實現(xiàn)鈦合金等溫成形與動態(tài)再結晶演化耦合響應的統(tǒng)一預測。本發(fā)明通過結合元胞自動機與晶體塑性有限元法,考慮了鈦合金材料在熱變形過程中不均勻變形、力學響應與動態(tài)再結晶之間的強烈耦合作用,實現(xiàn)了鈦合金等溫成形晶粒尺度不均勻變形、動態(tài)再結晶組織形態(tài)演變、再結晶晶粒尺寸演化、再結晶動力學、變形體和晶粒的流變應力的同步預測?;诎瑑上嗑ЯEc晶界的初始組織,建立鈦合金等溫成形三維有限元模型。其中,元胞自動機與晶體塑性有限元共用網(wǎng)格,即每個有限元為一個元胞。通過晶體塑性有限元模型計算晶粒尺度的不均勻變形與力學響應、以及不均勻變形導致的晶粒取向演化與位錯密度演化。其中,位錯密度與晶粒取向等變形信息被傳遞給元胞自動機用于計算動態(tài)再結晶演化?;诰w塑性有限元計算的變形信息,通過采用三維26鄰居類型以及半概率性元胞轉(zhuǎn)換規(guī)則,建立元胞自動機模型以計算鈦合金動態(tài)再結晶組織演化。隨后,動態(tài)再結晶導致的晶粒與晶界形態(tài)演化、晶粒取向演化、位錯密度演化、以及晶粒尺寸演化將被傳遞給晶體塑性有限元進行下一增量步的變形與力學響應計算,進而實現(xiàn)不均勻變形、力學響應與動態(tài)再結晶演化的緊密耦合。同時,由于元胞自動機采用有限元的變形時間,不僅使得組織演化時間具備物理意義,同時也保證了變形、應力響應與組織演化的高度同步性。元胞自動機與有限元的結合,使得該模型不僅可通過有限元分析軟件動態(tài)輸出位錯密度、應力應變分布、流動應力等變形信息,分別如附圖5、8、9、11所示,從附圖5中不同應變量的位錯密度分布可以看出,在不同的變形條件下位錯密度分布并不均勻;同時可以可視化輸出晶粒尺寸、再結晶動力學等組織演化信息,如附圖10、12所示,附圖10中可以看出再結晶的形成使平均晶粒尺寸降低,晶粒得到了細化,附圖12中不同溫度不同應變速率下的再結晶動力學曲線,可以看出再結晶體積分數(shù)隨著應變的增加而增加,呈現(xiàn)典型的“S”型曲線,這與實際情況相符;此外,附圖7中等效塑性應變與再結晶平均半徑對比圖表明了變形與再結晶組織演化的相互影響。因此,該模型有效的實現(xiàn)了變形與組織演化的統(tǒng)一預測,這對實現(xiàn)鈦合金構件等溫成形和組織性能的有效控制的具有重要的理論意義和工業(yè)指導價值。附圖說明圖1為本發(fā)明耦合模型流程圖;圖2為耦合模型示意圖;圖3為鈦合金高溫變形時晶界的軟化作用;圖4為三維26鄰居類型;圖5為位錯密度演化,其中,圖5a應變?yōu)?.02,圖5b應變?yōu)?.1,圖5c應變?yōu)?.2,圖5d應變?yōu)?.5;圖6為再結晶晶粒平均長大速度,其中,圖6a應變速率為1s-1的再結晶晶粒平均長大速度,圖6b應變速率為0.01s-1的再結晶晶粒平均長大速度;圖7為等效塑性應變與再結晶平均半徑對比圖,其中,圖7a是溫度在1323K應變速率為0.01s-1下應變量為0.01的等效塑性應變分布,圖7b是溫度在1323K應變速率為0.01s-1下應變量為0.01的平均晶粒半徑;圖8為變形條件下的應力分布圖,其中,圖8a是溫度為1323K、應變速率為0.01s-1、應變?yōu)?.05時的MISES應力圖8b是溫度為1323K、應變速率為0.01s-1、應變?yōu)?.05時的平均晶粒尺寸;圖9為變形條件下的應變分布圖,其中,圖9a是等效塑性應變分布圖,圖9b是平均晶粒尺寸分布圖;圖10為平均晶粒尺寸變化;圖11為流變應力曲線,其中,圖11a是溫度為1273K時不同應變速率下的流動應力,圖11b是溫度為1323K時不同應變速率下的流動應力;圖12為再結晶體積分數(shù)變化曲線,其中,圖12a是溫度為1273K時不同應變速率下的再結晶體積分數(shù),圖12b是溫度為1273K時不同應變速率下的再結晶體積分數(shù)。圖13是本發(fā)明的流程圖。圖中:1.三維微觀組織模型;2.晶體塑性模型;3.3D元胞自動機算法;4.第一鄰居類型;5.第二鄰居類型;6.第三鄰居類型;7.元胞鄰居;8.中心元胞。具體實施方式本實施例具體是一種TA15鈦合金等溫壓縮與動態(tài)再結晶演化耦合響應的預測方法。本實施例的實施基于Abaqus軟件平臺,并開發(fā)了用戶材料子程序。步驟3~13的均是通過用戶材料子程序來實現(xiàn)的,所述步驟3~12為一個時間增量步的具體計算內(nèi)容,所有時間增量步的計算完成后,則實現(xiàn)了TA15鈦合金等溫壓縮與動態(tài)再結晶演化的耦合響應。本實施例所述的TA15鈦合金相關擬合參數(shù)如表1所示。表1擬合參數(shù)c1(α)c1(β)c20(α)c20(β)c3(α)c3(β)c4c5c68.7×1069.1×106210019005.1×1032.1×1030.54.2×1030.5本實施例的具體實施步驟包括:步驟1,生成α+β兩相鈦合金等軸晶初始組織:首先通過元胞自動機生成規(guī)格為80×80×80、α相體積分數(shù)為22%,晶??倲?shù)為40的等軸晶初始組織。用不同顏色區(qū)分α相與β相的不同晶粒和晶界。步驟2,建立包含晶粒和晶界的鈦合金等溫成形三維有限元模型:將步驟1生成的α+β兩相鈦合金等軸晶初始組織信息保存為dat格式文件,并將該文件導入ABAQUS軟件,生成包含α+β兩相鈦合金等軸晶組織的變形體。采用立方體單元對所述變形體劃分網(wǎng)格,從而建立有限元幾何模型。網(wǎng)格尺寸為1.25×1.25×1.25μm3。下述的晶體塑性有限元方法和元胞自動機共用該有限元幾何模型,即每個有限元單元也就是一個元胞。對該有限元幾何模型中的α相單元和β相單元分別賦予材料參數(shù),所述相關材料參數(shù)見表2。該有限元幾何模型采用周期性邊界條件,加載方式為單軸壓縮。從而建立了包含晶粒和晶界的鈦合金等溫成形三維有限元模型。表2相關材料參數(shù)步驟3,基于ABAQUS/Explicit的用戶材料子程序VUMAT接口,讀取相關數(shù)據(jù):基于ABAQUS/Explicit的用戶材料子程序VUMAT接口,讀取各有限單元上一增量步的變形梯度、拉伸張量U*和晶粒滑移系位錯密度ρa、晶粒半徑、晶粒取向Q、相信息參數(shù)Ph、晶界參數(shù)Bdy、格林應變的共軛應力T*、滑移系a上滑移方向矢量ma、滑移系a上滑移面單位矢量na以及當前增量步的變形梯度。所述晶?;葡滴诲e密度ρa的初始位錯密度取109m-2;所述滑移系滑移方向ma、滑移面矢量na均位于晶體軸坐標系中。若讀取的相信息參數(shù)Ph為1則采用α相參數(shù)進行后續(xù)步驟的計算;若為讀取的相信息參數(shù)Ph為0則采用β相參數(shù)進行后續(xù)步驟的計算。若讀取的晶界參數(shù)Bdy為0表示非晶界元胞,若讀取的晶界參數(shù)Bdy為1表示晶界元胞。步驟4,確定晶粒間不均勻變形、單元的應力響應和晶粒取向演化:為了描述晶粒間不均勻變形,每一晶粒都被分為若干個有限單元,同一晶粒內(nèi)的有限單元被賦予相同取向,而表示不同晶粒的有限單元的取向不同;采用晶體塑性本構模型進行計算,由此晶粒間和晶粒內(nèi)的不均勻變形得以實現(xiàn)。所述不均勻變形指應變在晶粒間和晶粒內(nèi)的不均勻分布。在確定晶粒間不均勻變形、單元的應力響應和晶粒取向演化之前首先需要計算分解剪應力τa和滑移系抗力sa。步驟4的具體過程是:第一步、根據(jù)公式確定滑移系分解剪應力τa,其中T*為格林應變的共軛應力,其中:為Schmid張量,τa是滑移系分解剪應力。第二步、根據(jù)位錯密度計算滑移系抗力sa其中,s0為初始滑移抗力,sd為位錯交互作用對滑移抗力的影響,sHP為霍爾佩奇效應對滑移抗力的影響,λ為晶界軟化因子。初始滑移抗力表示為變形溫度的函數(shù):其中,c3為與固溶強化相關的強度系數(shù),c6為與材料相關的參考溫度,θ為單元溫度。位錯交互作用對滑移抗力的影響sd為:其中,c4為材料常數(shù),其值在0.1~1之間;b是泊氏矢量;t-△t指上一增量步,相應的t則指的是當前增量步;μ為剪切彈性模量,與溫度有關,通過公式(4)確定:霍爾佩奇效應sHP代表的晶粒尺寸對變形的阻礙作用表示為:其中,c5為霍爾佩奇系數(shù),r為晶粒半徑。鈦合金晶界在高溫變形中的作用如圖3所示,通過公式(6)計算軟化因子:其中,θmelt為材料熔點;為等效塑性應變;為宏觀應變速率。第三步、計算剪切應變速率其中,γ0為參考剪切應變速率,χ為率敏感因子。第四步、計算變形梯度的塑性部分、非塑性部分和格林應變:總的變形梯度F表示為:F=F*·Fp(8)式中F*表示晶格畸變和剛性轉(zhuǎn)動所產(chǎn)生的變形梯度,即非塑性部分;Fp則表示晶體沿著滑移方向的均勻剪切所對應的變形梯度,即塑性部分。塑性應變梯度變化率表示為:其中,Lp為速度梯度的塑性部分,由下式計算:由(8)式有:F*=F·(Fp)-1(11)通過公式(12)得到格林應變:其中,I為二階identity張量。第五步、通過彈性本構關系計算單元的柯西應力T:其中,T*為格林應變E*的共軛應力,為四階彈性張量。根據(jù)下式計算柯西應力T:第六步、計算晶粒取向的轉(zhuǎn)動:變形過程中,晶粒除了發(fā)生塑性剪切應變,還會產(chǎn)生剛性轉(zhuǎn)動,使得晶粒取向演變。通過公式(15)確定晶粒取向演化:Q=R*Q(R*)T,(15)其中,Q是代表晶粒取向的三個歐拉角表示的旋轉(zhuǎn)張量,R*代表材料晶格的剛性轉(zhuǎn)動,與非塑性變形梯度有關。所述R*通過下式計算:F*=R*U*,(16)其中U*為拉伸張量。至此,確定了晶粒間的不均勻變形、應力響應和晶粒取向演化。步驟5,計算晶粒的位錯密度演化;根據(jù)晶粒的滑移剪切應變速率計算晶粒的位錯密度演化。同時考慮動態(tài)再結晶與變形中的動態(tài)回復,通過公式(17)計算位錯密度:其中,ki為由于再結晶軟化產(chǎn)生的位錯密度修正系數(shù),ρa+為可動位錯不動化造成的位錯密度增加,即加工硬化效應。ρa-為位錯攀移、異號位錯相消造成的位錯泯滅。ρa+和ρa-分別通過公式(18)和(19)計算:其中,(18)和(19)式中林位錯與不動位錯密度存在如下關系:其中,N為滑移系總數(shù);m與n分別為位錯滑移方向與滑移面法向方向;為滑移系b的不動位錯密度。步驟6,模擬動態(tài)再結晶演化。將晶粒位錯密度作為變量傳遞給元胞自動機,計算動態(tài)再結晶演化。具體過程是:第一步、確定元胞狀態(tài)變量:位錯密度狀態(tài)變量:每個元胞的位錯密度為以及滑移系位錯密度為相狀態(tài)變量Ph:用于標定元胞的相信息,Ph=1為α相,Ph=0為β相;再結晶狀態(tài)變量Drx:用于標定元胞是否為新生成的再結晶相,Drx=1表示該元胞為再結晶相,Drx=0表示該元胞為母相;再結晶潛在形核狀態(tài)變量Potential:若母相元胞未轉(zhuǎn)換為再結晶潛在形核元胞,則Potential=0;否則,Potential=1;晶界狀態(tài)變量Bdy:用于標定元胞是否在晶界處,具體定義規(guī)則與步驟3中一致;晶粒取向狀態(tài)變量Q:描述晶粒取向的張量;晶粒尺寸狀態(tài)變量r:該晶粒的平均晶粒半徑;晶粒編號狀態(tài)變量Grain:包含母相晶粒與新生成的再結晶晶粒,每個晶粒都有不同的編號,處于同一個晶粒的元胞編號相同,處于不同晶粒的元胞編號不同。第二步、根據(jù)形核規(guī)則判斷是否形核;當變形基體內(nèi)位錯密度與臨界位錯密度滿足關系式ρi≥ρc時,新的無應變的晶核將以形核率在變形嚴重的區(qū)域形核,則該元胞轉(zhuǎn)換為t時刻潛在形核元胞,即有:其中,Qint為界面能;l為位錯自由程;Qline為位錯線能量;M為晶界遷移率,M為:其中,δD0b為特征晶界厚度與絕對0度晶界自擴散系數(shù)之積;KB波爾茲曼常數(shù);Qdiffu自擴散激活能;R為氣體常數(shù);b為柏氏矢量。通過公式(23)計算位錯線能量Qline:形核率由公式(24)計算:其中,CN為擬合參數(shù),m為再結晶形核率指數(shù),Qact為形核激活能,θ為溫度。為保證在變形嚴重區(qū)域優(yōu)先形核,根據(jù)每個元胞的位錯密度值,引入形核概率Pnuclei(i)來描述潛在形核元胞i轉(zhuǎn)變?yōu)樵俳Y晶晶核的概率,Pnuclei(i)計算為:其中,ρ(i)為t時刻潛在形核元胞i的位錯密度,ρmax為t時刻潛在再結晶形核元胞中最大位錯密度。隨機選取N(t)個t時刻潛在再結晶形核元胞并生成隨機數(shù)ξ,如果ξ≤Pnuclei(i),則該元胞轉(zhuǎn)換為再結晶晶核元胞,即有:第三步、再結晶長大;一旦元胞開始形核,就會以速率v向其臨近元胞長大,考慮單獨形核和集中形核兩種情況,對與每一個母相元胞,計算其被相鄰再結晶元胞吞噬的概率:(i)若中心母相元胞i只有一個再結晶元胞鄰居j,長大距離si,j通過公式(27):其中,t1為上一次si,j置零的時間,晶界遷移的速度v為:vi,j=MP(28)其中,M為晶界遷移率,P為晶界遷移驅(qū)動力。晶界遷移驅(qū)動力P為:P=Pd-Pr(29)其中,Pd為促進晶界遷移的驅(qū)動力,Pr為阻礙晶界遷移的驅(qū)動力。Pd為:其中,ρM與ρR分別為母相與再結晶相的位錯密度。Pr為:req為晶界等效曲率半徑,Qm大角度晶界能。等效曲率半徑為:其中,Ni為晶粒編號Grain=i的元胞總數(shù)目,Vcell為單個元胞所代表的實際變形組織的體積。大角度晶界能可計算為:其中,Om為晶粒取向差,v為泊松比,μ為剪切模量。對于元胞i與元胞j,晶粒取向差可以計算為:其中,Qi與Qj分別為元胞i與元胞j的晶粒取向矢量矩陣。如圖4所示,中心元胞易被第一鄰居類型4吞噬轉(zhuǎn)換為再結晶元胞,第二鄰居類型5次之,最不容易被第三鄰居類型6吞噬并轉(zhuǎn)換為再結晶元胞。同時,再結晶元胞的等效曲率半徑越大,中心母相元胞則越難被再結晶的元胞鄰居7吞噬成為再結晶元胞。因此,引入球形膨脹概率因子Pi,j來描述中心元胞8被再結晶鄰居吞噬轉(zhuǎn)換為再結晶元胞的概率,Pi,j計算為:其中,r0為參考半徑,0.98、0.57與0.17分別表示為以中心元胞的為球心,以1.5r0為半徑的球體被鄰居元胞切割的體積與單位元胞的體積的比值。如果si,j≥l,則生成隨機變量ζ∈[0,1]。若ζ≤Pi,j,則中心元胞i轉(zhuǎn)換為再結晶元胞,長大距離狀態(tài)變量si,j置零,中心母相元胞i的位錯密度狀態(tài)變量、相狀態(tài)變量、再結晶狀態(tài)變量、晶粒取向狀態(tài)變量以及晶粒編號狀態(tài)變量均與相鄰再結晶元胞j的狀態(tài)變量相等。如果si,j<l,則長大距離狀態(tài)變量si,j隨時間t繼續(xù)積累。(ii)中心元胞有多個再結晶鄰居依據(jù)(i)中的步驟對每個鄰居都進行判斷。若中心元胞滿足能夠同時被多個鄰居吞噬的條件,則優(yōu)先被具有較大Pi,j的再結晶元胞吞噬。具體規(guī)則如下所示:(1)若中心元胞具有n個再結晶元胞鄰居,則記錄該中心的所有再結晶元胞鄰居{j1,j2,......,jn}。(2)計算中心元胞i對所有再結晶元胞鄰居{j1,j2,......,jn}的生長概率{Pgrowth(1),Pgrowth(2),......,Pgrowth(n)}。(3)從再結晶元胞鄰居{j1,j2,......,jn}選取最大Pgrowth對應的鄰居元胞jx,計算長大距離si,j,且生成隨機變量ζ∈[0,1]。若si,j>l且ζ≤Pi,j,則中心元胞被元胞jx吞噬。若不滿足條件,則再結晶元胞鄰居集{j1,j2,......,jn}去掉元胞jx元素,生長概率{Pgrowth(1),Pgrowth(2),......,Pgrowth(n)}去掉Pgrowth(x)。(4)重復(3)步驟。如果si,j<l,則長大距離狀態(tài)變量si,j隨時間t繼續(xù)積累。第四步、晶界的演化;元胞的形核及長大都會影響晶界的演化,因此需要計算每次形核和長大發(fā)生后的晶界演化。其方法為:判斷中心元胞與鄰居元胞的晶粒編號狀態(tài)變量Grain是否相等,即判斷是否滿足:Grain(j)=Grain(i);j∈{元胞i的所有鄰居}(36)若滿足上述條件,則該元胞處于晶粒內(nèi)部,晶界狀態(tài)變量Bdy=0;若不滿足則該元胞處于晶界上,即有晶界狀態(tài)變量Bdy=1。至此,完成動態(tài)再結晶演化的模擬。步驟7,更新晶粒的位錯密度;根據(jù)模擬得到的動態(tài)再結晶演化更新晶粒的位錯密度。步驟8,確定位錯密度修正系數(shù);步驟9,確定再結晶體積分數(shù);式中,Xnew為新生成的再結晶晶粒,即Drx=1的元胞所占元胞數(shù)目,X為元胞空間總元胞數(shù)目。步驟10,確定當前增量步變形體的流變應力σ;通過公式(41)計算流變應力并輸出:其中Ti為每一個有限元單元的應力響應,NG為晶粒數(shù)目;步驟11,存儲公共變量;將更新后的相信息Ph、晶界參數(shù)Bdy、位錯密度ρi、晶粒尺寸req、再結晶體積分數(shù)f作為公共變量存儲,以便于下一增量步采用晶體塑性有限元模型2計算下一時刻的不均勻變形;步驟12,當前時刻晶體塑性有限元與元胞自動機的一次耦合。輸出動態(tài)再結晶的組織形態(tài)、再結晶晶粒尺寸、流變應力曲線、再結晶體積分數(shù)及其隨變形的演化;至此,完成了當前時刻晶體塑性有限元與元胞自動機的一次耦合。步驟13,返回有限元模型,重復步驟3~12,進行下一增量步的計算,直至完成鈦合金等溫成形與動態(tài)再結晶演化耦合響應的預測。在每次重復進行下一增量步計算時,讀取各有限元單元前一時刻的變形梯度、當前時刻的變形梯度、拉伸張量U*、晶?;葡滴诲e密度ρa、晶粒半徑、相信息參數(shù)Ph、晶界參數(shù)Bdy、格林應變的共軛應力T*以及晶體軸坐標系中的滑移系滑移方向與滑移面矢量ma和na。通過本實施例,能夠獲得如下預測結果:1、位錯密度的演化。圖5是溫度為1323K應變速率為0.01s-1下不同應變量的位錯密度分布。在材料變形的初期階段,晶界的位錯密度增殖更快,而基體晶粒內(nèi)部的位錯密度增殖速度較慢,這是因為:晶界的軟化作用使得晶界的材料變形更加劇烈,同時晶界兩側的晶粒由于晶粒取向與變形抗力存在差異,晶界的協(xié)調(diào)作用使晶界的變形量更大,兩者的共同作用導致晶界的位錯密度增殖更快;同時,由于初期階段晶界對變形協(xié)調(diào)的貢獻較大,使得基體晶粒內(nèi)部的變形較小,位錯密度增殖速度較慢。隨著變形量的增加,基體晶粒的位錯密度逐漸增加,部分基體晶粒的位錯密度達到臨界位錯密度發(fā)生動態(tài)再結晶,從而造成位錯密度的降低。隨著變形量的繼續(xù)增加,基體晶粒的位錯密度達到飽和值,再結晶晶粒由于變形造成位錯密度逐漸增加且再結晶晶粒的位錯密度與基體晶粒的位錯密度差值逐漸減小。隨著變形量進一步增加,再結晶晶粒的位錯密度增加并趨近于基體晶粒的位錯密度,整體的位錯密度趨于穩(wěn)定。2、再結晶晶粒平均長大速度。圖6中(a)和(b)所示分別為溫度在1273K應變速率為1s-1與0.01s-1下的再結晶晶粒平均長大速度。在變形的初期階段,再結晶平均晶粒尺寸的平均增長速率為零,這是因為基體晶粒的位錯密度較小,均未達到臨界位錯密度,不足以滿足再結晶形核條件。隨著變形量的增加,母相急劇大量形核,且母相位錯密度與新生成的再結晶位錯密度差值較大,為再結晶的長大提供了較大的驅(qū)動力,再結晶快速長大,再結晶平均晶粒尺寸的增長速率快速增加。隨著變形量的增加,再結晶形核數(shù)目增長速度逐漸變慢,新生成的再結晶由于變形而導致位錯密度逐漸增加,而基體晶粒位錯密度逐漸進入飽和而不發(fā)生變化,再結晶晶粒的位錯密度與基體晶粒位錯密度的差值逐漸降低,再結晶的驅(qū)動力逐漸減小,進而導致再結晶平均長大速率呈現(xiàn)降低的趨勢。3、等效塑性應變分布與平均晶粒尺寸分布對比圖。圖7所示為溫度在1323K應變速率為0.01s-1下應變量為0.01的等效塑性應變分布(a)與平均晶粒半徑對比圖(b)。從圖中可以看出,再結晶的形核分布并不均勻,再結晶形核位置主要集中在等效塑性應變較大的晶界處。形量大的區(qū)域并非一定形核,這主要有兩點原因:首先,位錯密度的演化速度,如位錯增殖與湮滅主要與材料的瞬時變形速率相關,材料的瞬時變形速率越大,位錯演化的速率越大,而材料的變形程度只反映材料變形隨時間的累積程度;其次,再結晶形核是一個非穩(wěn)態(tài)的熱激活過程,其形核過程具有隨機性。4、應力分布圖。圖8所示為溫度在1323K應變速率為0.01s-1下應變量為0.05的應力分布圖與平均晶粒尺寸分布圖。通過對比圖8(a)與(b)可以發(fā)現(xiàn),不連續(xù)動態(tài)再結晶對鈦合金變形組織的應力分布有較大的影響,在動態(tài)再結晶晶粒的區(qū)域呈現(xiàn)出較低的應力,呈現(xiàn)“應力塌陷區(qū)”。5、應變分布圖。圖9為溫度為1323K應變速率為0.1s-1下真實應變?yōu)?.06的等效塑性應變分布與平均晶粒尺寸分布圖。從圖中可以看出,不連續(xù)動態(tài)再結晶對材料的等效塑性應變分布的影響較為明顯。在不連續(xù)動態(tài)再結晶發(fā)生的區(qū)域,等效塑性應變相對較大,而基體晶粒內(nèi)部的等效塑性應變相對較小。然而,在動態(tài)再結晶的大量聚集形核與長大的區(qū)域出現(xiàn)了變形量低于母相的“應變抑制區(qū)”。6、平均晶粒尺寸。圖10為溫度在1323k時不同應變速率下平均晶粒尺寸。從圖中可以看出,平均晶粒尺寸隨著變形量的增加而降低并達到穩(wěn)定值,晶粒得到細化。應變速率越高,平均晶粒尺寸越小,這是因為:在高應變速率下,材料的變形較劇烈促進再結晶大量形核,然而再結晶晶核沒有充足的時間長大,進而形成較小的再結晶晶粒。7、流動應力預測。圖11(a)和(b)分別為溫度在1273k和1323k時、不同應變速率下的流動應力預測,符號點代表實驗數(shù)據(jù),曲線為模擬值。在變形初始階段,流動應力迅速增加至峰值應力。隨著變形的增加,流動應力逐漸呈現(xiàn)軟化,這是因為變形導致了材料內(nèi)部溫度的升高以及再結晶的軟化作用。從圖中可以看出,在同一個溫度下,應變速率越高,流動應力越高;同一個應變速率,變形溫度越高,流動應力越低。8、再結晶體積分數(shù)預測。圖12中(a)和(b)分別為TA15鈦合金在溫度1273K和1323K時、不同應變速率下的再結晶動力學曲線,圖中符號點代表實驗數(shù)據(jù),曲線為模擬值。從圖中可以看出,再結晶體積分數(shù)隨著應變的增加而增加,呈現(xiàn)“S”型曲線。通過對比同一溫度同一應變量下不同應變速率的再結晶體積分數(shù)可以看出,應變速率對再結晶體積分數(shù)有較大的影響,應變速率越高,再結晶體積分數(shù)越。而在相同的應變速率下,溫度越高,再結晶體積分數(shù)越高。當前第1頁1 2 3