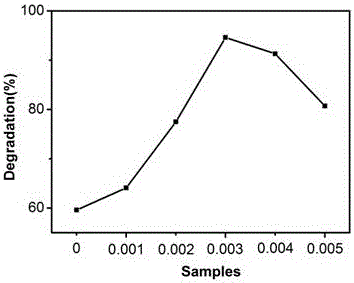
本發(fā)明屬于納米材料制備
技術(shù)領(lǐng)域:
,更具體地,涉及一種微量鐵摻雜的三氧化鎢納米纖維光催化劑的制備方法。
背景技術(shù):
:近年來,隨著工業(yè)化進程的發(fā)展和人們生活水平的迅速提高,環(huán)境污染問題成為目前人類面臨的主要難題,尤其是水體污染,越來越多的引起大家的關(guān)注。水體污染源中,工業(yè)廢水占很大一部分,因其顏色深,毒性強,很難處理。半導(dǎo)體光催化劑以其穩(wěn)定的物理化學(xué)性質(zhì),在地球上分布廣泛,容易獲得,廉價和無二次污染等優(yōu)點得到了廣泛研究。傳統(tǒng)的半導(dǎo)體光催化劑研究最多的就是二氧化鈦(TiO2)和氧化鋅(ZnO),它們的帶隙較寬,對波長較短的紫外光有很好的響應(yīng),但是由于紫外光在太陽光中僅占少部分所以實際應(yīng)用受到了限制。作為過渡金屬氧化物的一員,氧化鎢(WO3)是一種間接帶隙n型半導(dǎo)體材料,其禁帶寬度是2.2~2.8eV,對于可見光有很好的吸收,因此是一種非常具有發(fā)展?jié)摿Φ陌雽?dǎo)體光催化劑。靜電紡絲技術(shù)是一種用于快速簡單制備納米纖維的方法,制造裝置簡單、紡絲成本低廉、可紡物質(zhì)種類繁多,不僅在實驗室研究方面有很大的進展,產(chǎn)業(yè)化潛力也非常巨大。因此靜電紡絲法批量制備三氧化鎢納米纖維并將其用作光催化劑有很大的工業(yè)價值和社會意義。但是單純的三氧化鎢光催化活性比較低,通過進行金屬摻雜可以提高其光催化性能。鐵元素在地球上分布廣泛,廉價易得,同時不會對水體造成二次污染,已有研究表明,在半導(dǎo)體光催化劑中摻入金屬離子,通過IFCT效應(yīng)可明顯抑制電子-空穴對的復(fù)合,提高光催化劑的催化活性。技術(shù)實現(xiàn)要素:本發(fā)明的目的在于根據(jù)現(xiàn)有技術(shù)中三氧化鎢納米纖維作為催化劑中催化活性的不足,提供了一種微量鐵摻雜的三氧化鎢納米纖維光催化劑的制備方法。本發(fā)明的目的通過以下技術(shù)方案實現(xiàn):本發(fā)明提供了一種微量鐵摻雜的三氧化鎢納米纖維光催化劑的制備方法,包括如下步驟:S1.將偏鎢酸銨溶于水,加入聚乙烯吡咯烷酮,攪拌得到前驅(qū)體溶液;S2.將S1中前驅(qū)體溶液進行靜電紡絲,得到初紡纖維;S3.將S2中制備得到的初紡纖維煅燒,冷卻后得到三氧化鎢納米纖維;S4.將S3中三氧化鎢納米纖維浸漬在鐵鹽溶液中,干燥后得到所述光催化劑;S1中,偏鎢酸銨與水的固液比為(0.2~0.6):1;所述聚乙烯吡咯烷酮的分子量為(1~2)×106;聚乙烯吡咯烷酮與水的固液比為(0.1~0.3):1;S2步驟靜電紡絲中,電壓為18~30KV,接收距離為15cm,推進速度為0.01~0.1ml/min;S4中,鐵鹽溶液的濃度為0.03~0.3g/L,鐵相對于三氧化鎢的質(zhì)量分?jǐn)?shù)為0.1~1%。本發(fā)明首先通過將偏鎢酸銨溶于水,加入聚乙烯吡咯烷酮,調(diào)控各原料之間的比例,得到前驅(qū)體溶液,然后通過靜電紡絲工藝,將上述具備較好的導(dǎo)電性和粘度的前驅(qū)體溶液制成初紡纖維,經(jīng)過煅燒后,通過摻雜微量鐵制備得到光催化性能得到提升的三氧化鎢納米纖維。優(yōu)選地,鐵相對于三氧化鎢的質(zhì)量分?jǐn)?shù)為0.3%。優(yōu)選地,S1中聚乙烯吡咯烷酮的分子量為1.3×106。本發(fā)明中PVP的作用是為了與偏鎢酸銨配合,兩者在恰當(dāng)配比下增加前驅(qū)體溶液的粘度和導(dǎo)電性用來靜電紡絲,同時在成纖維以后快速固化過程中也可以起到支撐的作用保持纖維的形貌。優(yōu)選地,S1中,偏鎢酸銨與水的固液比為(0.35~0.5):1;聚乙烯吡咯烷酮與水的固液比為(0.1~0.25):1。優(yōu)選地,S1中攪拌時間為攪拌2~5小時。優(yōu)選地,S3中煅燒溫度為500~650℃,升溫速度為1~5℃/min,并保溫0.5小時。優(yōu)選地,S4中浸漬溫度為80~90℃,浸漬時間為2~4小時。優(yōu)選地,干燥溫度為110℃,干燥時間為5~8小時。優(yōu)選地,所述鐵鹽為氯化鐵。本發(fā)明中提及的“固液比”為重量份和體積份之間的關(guān)系,以g/ml計。與現(xiàn)有技術(shù)相比,本發(fā)明具有以下優(yōu)點及有益效果:本發(fā)明制備方法簡單,成本低廉,采用水作為溶劑,綠色環(huán)保;結(jié)合靜電紡絲技術(shù)和浸漬法,操作簡單,該方法制得的微量鐵摻雜三氧化鎢并未改變?nèi)趸u的網(wǎng)絡(luò)狀分布,形貌穩(wěn)定,直徑分布均勻,同時極大地提高了三氧化鎢的光催化降解性能。附圖說明圖1是實施例1制得的三氧化鎢納米纖維和鐵摻雜之后的三氧化鎢的SEM圖。圖2是實施例1制備的微量鐵摻雜三氧化鎢納米纖維的TEM-mapping圖圖3是實施例1制備的三氧化鎢納米纖維和鐵摻雜之后的三氧化鎢的XRD圖。圖4是使用本發(fā)明方法制備的鐵摻雜三氧化鎢作為光催化劑對甲基橙進行降解的降解效果圖。圖5是使用本發(fā)明方法中不同的微量鐵摻雜量制備得到的的光催化劑對甲基橙進行降解的降解效果對比圖。圖6是對比例1中制備得到的鐵摻雜三氧化鎢的SEM圖。圖7是對比例2中制備得到的鐵摻雜三氧化鎢的SEM圖。圖8是對比例3中制備得到的鐵摻雜三氧化鎢的SEM圖。具體實施方式以下結(jié)合具體實施例和附圖來進一步說明本發(fā)明,但實施例并不對本發(fā)明做任何形式的限定。除非特別說明,本發(fā)明采用的試劑、方法和設(shè)備為本
技術(shù)領(lǐng)域:
常規(guī)試劑、方法和設(shè)備。除非特別說明,本發(fā)明所用試劑和材料均為市購。實施例1將3.5g市售的偏鎢酸銨溶于10ml去離子水中,加入分子量為1300000的聚乙烯吡咯烷酮(PVP),加入量為1g,攪拌至溶液呈均勻透明后得到前驅(qū)體溶液;隨后通過單軸靜電紡絲法,電壓20KV,接收距離15cm,推進速度0.02ml/min,得到白色布狀初紡纖維;將初紡纖維置于管式爐中抽真空600℃煅燒,升溫速度3℃/min,保溫0.5小時,自然冷卻至室溫,得到三氧化鎢納米纖維。配制0.03g/L的FeCl3溶液,取50ml加入0.5g氧化鎢納米纖維,在加熱臺上以85℃浸泡3小時后過濾,最后在110℃鼓風(fēng)干燥箱中干燥5小時,得到微量鐵摻雜的三氧化鎢納米纖維。通過該實施例制備得到的光催化劑進行SEM、TEM-mapping、XRD表征,結(jié)果如圖1~3所示。其中,圖1(a)為制得的三氧化鎢納米纖維網(wǎng)狀分布的SEM圖。圖1(b)為進行微量鐵摻雜處理之后的SEM圖??梢钥闯鲞M行鐵摻雜處理并沒有影響三氧化鎢納米纖維的網(wǎng)狀形貌。圖2是使用該方法制備的微量鐵摻雜三氧化鎢納米纖維的TEM-mapping圖。在圖2中,可以看出鎢、氧、鐵三種元素均勻地分布在氧化鎢納米纖維上面。圖3是使用該方法制備的純?nèi)趸u和微量鐵摻雜三氧化鎢的XRD圖。在圖3中,衍射角在23.1,23.5,24.3,26.5,28.9,33.2,34.1和41.9°處的峰分別屬于單斜晶型氧化鎢(002),(020),(200),(120),(112),(022),(202)和(222)晶面的衍射??梢钥闯鲋苽涞漠a(chǎn)物就是三氧化鎢,且結(jié)晶性良好。進行鐵摻雜之后衍射峰并未出現(xiàn)改變,可見摻雜微量的鐵并不會改變?nèi)趸u的晶型結(jié)構(gòu)。實施例2將3.5g水合偏鎢酸銨溶于10ml去離子水中,加入分子量為1300000的聚乙烯吡咯烷酮(PVP),加入量為1.5g,攪拌至溶液呈均勻透明后得到前驅(qū)體溶液;隨后通過單軸靜電紡絲法,電壓20KV,接收距離15cm,推進速度0.02ml/min,得到初紡纖維;將初紡纖維置于管式爐中抽真空600℃煅燒,升溫速度2℃/min,保溫0.5小時,自然冷卻至室溫,得到三氧化鎢納米纖維。配制0.06g/L的FeCl3溶液,取50ml加入0.5g氧化鎢納米纖維,在加熱臺上以85℃浸泡3小時后過濾,最后在110℃鼓風(fēng)干燥箱中干燥5小時,得到微量鐵摻雜的三氧化鎢納米纖維。實施例3將5.0g水合偏鎢酸銨溶于10ml去離子水中,加入分子量為1300000的聚乙烯吡咯烷酮(PVP),加入量為1.5g,攪拌至溶液呈均勻透明后得到前驅(qū)體溶液;隨后通過單軸靜電紡絲法,電壓24KV,接收距離15cm,推進速度0.02ml/min,得到初紡纖維;將初紡纖維置于管式爐中抽真空550℃煅燒,升溫速度2℃/min,保溫0.5小時,自然冷卻至室溫,得到三氧化鎢納米纖維。配制0.09g/L的FeCl3溶液,取50ml加入0.5g氧化鎢納米纖維,在加熱臺上以80℃浸泡3小時后過濾,最后在110℃鼓風(fēng)干燥箱中干燥6小時,得到微量鐵摻雜的三氧化鎢納米纖維。實施例4將3.5g水合偏鎢酸銨溶于10ml去離子水中,加入分子量為1300000的聚乙烯吡咯烷酮(PVP),加入量為2.5g,攪拌至溶液呈均勻透明后得到前驅(qū)體溶液;隨后通過單軸靜電紡絲法,電壓24KV,接收距離15cm,推進速度0.02ml/min,得到初紡纖維;將初紡纖維置于管式爐中抽真空600℃煅燒,升溫速度2℃/min,保溫0.5小時,自然冷卻至室溫,得到三氧化鎢納米纖維。配制0.12g/L的FeCl3溶液,取50ml加入0.5g氧化鎢納米纖維,在加熱臺上以85℃浸泡3小時后過濾,最后在110℃鼓風(fēng)干燥箱中干燥6小時,得到微量鐵摻雜的三氧化鎢納米纖維。實施例5將3.5g水合偏鎢酸銨溶于10ml去離子水中,加入分子量為1300000的聚乙烯吡咯烷酮(PVP),加入量為2.5g,攪拌至溶液呈均勻透明后得到前驅(qū)體溶液;隨后通過單軸靜電紡絲法,電壓30KV,接收距離15cm,推進速度0.05ml/min,得到初紡纖維;將初紡纖維置于管式爐中抽真空600℃煅燒,升溫速度2℃/min,保溫0.5小時,自然冷卻至室溫,得到三氧化鎢納米纖維。配制0.15g/L的FeCl3溶液,取50ml加入0.5g氧化鎢納米纖維,在加熱臺上以90℃浸泡3小時后過濾,最后在110℃鼓風(fēng)干燥箱中干燥7小時,得到微量鐵摻雜的三氧化鎢納米纖維。對比例1:將5g水合偏鎢酸銨溶于10ml去離子水中,加入分子量為1300000的聚乙烯吡咯烷酮(PVP),加入量為1g,攪拌至溶液呈均勻透明后得到前驅(qū)體溶液;隨后通過單軸靜電紡絲法,電壓30KV,接收距離15cm,推進速度0.05ml/min,得到初紡纖維;將初紡纖維置于管式爐中抽真空600℃煅燒,升溫速度2℃/min,保溫0.5小時,自然冷卻至室溫,得到三氧化鎢。由于前驅(qū)體溶液并未在本發(fā)明配比范圍內(nèi),出現(xiàn)了如圖6的粘連情況。對比例2:將1g水合偏鎢酸銨溶于10ml去離子水中,加入分子量為1300000的聚乙烯吡咯烷酮(PVP),加入量為0.5g,攪拌至溶液呈均勻透明后得到前驅(qū)體溶液;隨后通過單軸靜電紡絲法,電壓30KV,接收距離15cm,推進速度0.05ml/min,得到初紡纖維;將初紡纖維置于管式爐中抽真空600℃煅燒,升溫速度2℃/min,保溫0.5小時,自然冷卻至室溫,得到三氧化鎢。由于前驅(qū)體溶液并未在本發(fā)明配比范圍內(nèi),出現(xiàn)了如圖7的珠粒。對比例3:將3.5g水合偏鎢酸銨溶于10ml去離子水中,加入分子量為1300000的聚乙烯吡咯烷酮(PVP),加入量為2.5g,攪拌至溶液呈均勻透明后得到前驅(qū)體溶液;隨后通過單軸靜電紡絲法,電壓15KV,接收距離10cm,推進速度0.2ml/min,得到初紡纖維;將初紡纖維置于管式爐中抽真空600℃煅燒,升溫速度2℃/min,保溫0.5小時,自然冷卻至室溫,得到三氧化鎢納米纖維。由于靜電紡絲參數(shù)不在本發(fā)明范圍內(nèi),出現(xiàn)了如圖8的情況,纖維彎曲,直徑分布不均。實施例6對甲基橙的光催化降解性能驗證:驗證方法:向反應(yīng)器中加入150ml濃度為10mg/L的甲基橙溶液,取50mg實施例1~5分別制得的微量鐵摻雜的三氧化鎢納米纖維投入其中(并以未摻雜的三氧化鎢納米纖維進行對比),暗反應(yīng)30min后達到吸附平衡,然后在300W氙燈下照射,每30min取一次樣,再用紫外-可見分光光度計測量溶液的吸光度并計算降解率。降解結(jié)果見圖4和表1所示,其中0.001-0.005分別代表的是相對鐵摻雜含量為0.1%-0.5%。圖5是不同的鐵摻雜量氧化鎢納米纖維的光催化效果對比,可以看出相對摻雜量為0.3%時催化效果提升最高。表1實施例1~5中制備得到的催化劑降解率實施例編號實施例1實施例2實施例3實施例4實施例5降解率(%)64.1%77.5%94.6%91%80.7%當(dāng)前第1頁1 2 3