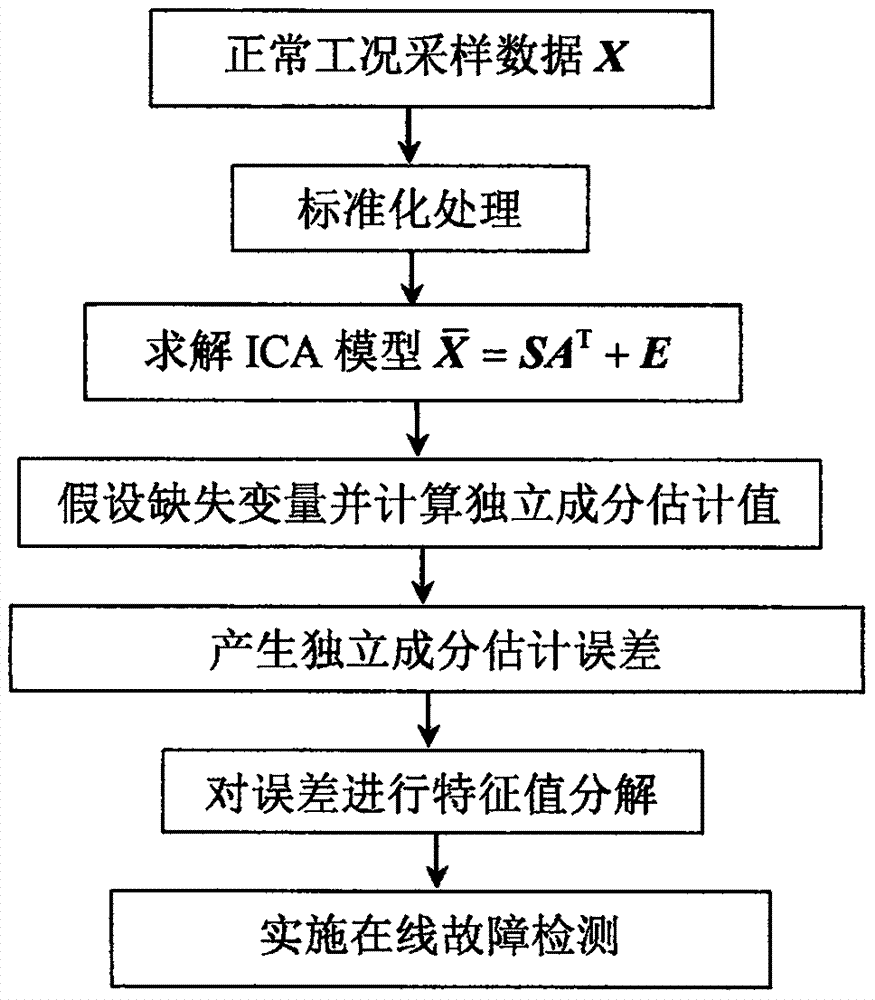
本發(fā)明涉及一種工業(yè)過程監(jiān)測方法,尤其是涉及一種基于缺失變量建模思路的非高斯過程監(jiān)測方法。
背景技術(shù):
:在工業(yè)生產(chǎn)流程中,確保生產(chǎn)過程持續(xù)處于正常工況對(duì)于保證產(chǎn)品質(zhì)量穩(wěn)定性具有重要意義。因此,具備故障檢測功能的過程監(jiān)測模塊在生產(chǎn)實(shí)際中必不可少,這也是學(xué)術(shù)界和工業(yè)界能一直持續(xù)不斷的針對(duì)過程監(jiān)測進(jìn)行理論與應(yīng)用研究的主要原因。從研究歷程上看,過程監(jiān)測從最開始的基于機(jī)理模型的故障檢測方法開始,已經(jīng)逐步演變成數(shù)據(jù)驅(qū)動(dòng)的故障檢測方法。相比于建立機(jī)理模型,數(shù)據(jù)驅(qū)動(dòng)的方法實(shí)施起來更加容易,更加適合于現(xiàn)代大型工業(yè)過程對(duì)象。當(dāng)前,工業(yè)“大數(shù)據(jù)”的趨勢下也在不斷地催生著新型數(shù)據(jù)驅(qū)動(dòng)的過程監(jiān)測方法。在這一研究領(lǐng)域中,多變量統(tǒng)計(jì)分析算法是被最廣泛使用的建模方法。其中,以主成分分析(principalcomponentanalysis,pca)與獨(dú)立成分分析(independentcomponentanalysis,ica)為基礎(chǔ)的故障檢測方法層出不窮,衍生出了各式各樣的、能適應(yīng)于不同類型工業(yè)對(duì)象的過程監(jiān)測方法。一般來講,基于pca的過程監(jiān)測模型大多都假設(shè)采樣數(shù)據(jù)服從近似高斯分布,從而可以方便地確定出描述正常數(shù)據(jù)變化范圍的控制上限。然而,現(xiàn)代工業(yè)過程對(duì)象的復(fù)雜性導(dǎo)致采樣數(shù)據(jù)不服從高斯分布。因此,傳統(tǒng)pca方法用于故障檢測時(shí)存在較為顯著的故障漏報(bào)率或誤報(bào)率。相比之下,ica算法可以挖掘出非高斯的獨(dú)立成分信息,更適合于監(jiān)測非高斯過程數(shù)據(jù)。而且,許多科研文獻(xiàn)也都通過實(shí)例驗(yàn)證了基于ica的方法優(yōu)越于基于pca的方法。在現(xiàn)有的科研與專利文獻(xiàn)中,確定ica故障檢測模型的控制限的方法主要依賴于核密度估計(jì)。從空間幾何結(jié)構(gòu)上看,該控制限其實(shí)定義了一個(gè)超球體的表面,所有位于超球體內(nèi)部的數(shù)據(jù)點(diǎn)都為正常工況數(shù)據(jù)。然而,由于數(shù)據(jù)本身的非高斯性,正常數(shù)據(jù)的分布范圍不可能全部填充該超球體。因此,位于超球體內(nèi)部的數(shù)據(jù)點(diǎn)不一定都是正常數(shù)據(jù)樣本。造成這一問題的因素主要源于ica模型提取的獨(dú)立成分本身是非高斯的。因此,就這一點(diǎn)問題上基于ica的非高斯過程監(jiān)測模型還需進(jìn)一步的改進(jìn)。值得注意的是,誤差一般都服從或近似服從高斯分布??墒牵`差的產(chǎn)生通常需要一個(gè)實(shí)際值與一個(gè)估計(jì)值,每個(gè)監(jiān)測樣本轉(zhuǎn)換成對(duì)應(yīng)的獨(dú)立成分后即可當(dāng)成ica模型的實(shí)際值。那么,如何產(chǎn)生獨(dú)立成分的估計(jì)值就是最關(guān)鍵的一個(gè)問題??上攵裟墚a(chǎn)生獨(dú)立成分的估計(jì)值,那么獨(dú)立成分實(shí)際值與估計(jì)值之間的誤差就可以獲得。而且,原始不服從高斯分布的獨(dú)立成分變成誤差后,也就服從高斯分布了,確定相應(yīng)的控制限就可以更精確地描述正常數(shù)據(jù)的分布范圍。在已有的研究文獻(xiàn)中,有部分學(xué)者在傳統(tǒng)pca的故障檢測模型中提出了缺失變量的處理方法,旨在解決生產(chǎn)實(shí)際中的采樣數(shù)據(jù)有可能會(huì)出現(xiàn)數(shù)據(jù)缺失的問題。缺失變量的方法主要通過已有的pca模型,利用已測量得到的數(shù)據(jù)在不需要缺失數(shù)據(jù)的前提下可以將相對(duì)應(yīng)的主成分信息估計(jì)出來。鑒于此,利用缺失變量處理的思路或許能為產(chǎn)生獨(dú)立成分的估計(jì)值提供一條可行的解決策略。技術(shù)實(shí)現(xiàn)要素:本發(fā)明所要解決的主要技術(shù)問題是:如何利用缺失變量的建模思路建立一個(gè)更可靠的非高斯過程監(jiān)測模型。為此,本發(fā)明提供了一種基于缺失變量建模思路的非高斯過程監(jiān)測方法。該方法在傳統(tǒng)ica模型的基礎(chǔ)上,通過逐一假設(shè)各個(gè)測量變量缺失數(shù)據(jù)后估計(jì)出相應(yīng)的獨(dú)立成分。然后,以獨(dú)立成分實(shí)際值與估計(jì)值之間的誤差做為被監(jiān)測對(duì)象,建立適當(dāng)統(tǒng)計(jì)量實(shí)施在線過程監(jiān)測。本發(fā)明解決上述技術(shù)問題所采用的技術(shù)方案為:一種基于缺失變量建模思路的非高斯過程監(jiān)測方法,包括以下步驟:(1)利用采樣系統(tǒng)收集生產(chǎn)過程正常運(yùn)行狀態(tài)下的樣本數(shù)據(jù),組成訓(xùn)練數(shù)據(jù)矩陣:x∈rn×m,并對(duì)x進(jìn)行標(biāo)準(zhǔn)化處理,使每個(gè)測量變量的均值為0,方差為1,得到新的數(shù)據(jù)矩陣其中,n為訓(xùn)練樣本數(shù),m為過程測量變量數(shù),r為實(shí)數(shù)集,rn×m表示n×m維的實(shí)數(shù)矩陣,為矩陣中第k個(gè)變量的n個(gè)測量數(shù)據(jù),k=1,2,…,m。(2)利用ica算法為建立ica模型,即:其中,為d個(gè)獨(dú)立成分列向量組成的矩陣,w∈rm×d為分離矩陣,a∈rm×d為混合矩陣,e∈rn×m表示模型誤差,上標(biāo)號(hào)t表示矩陣或向量的轉(zhuǎn)置。(3)假設(shè)矩陣中第k列數(shù)據(jù)缺失,其余可用列組成矩陣xk∈rn×(m-1),并利用如下所示公式計(jì)算得到獨(dú)立成分矩陣的估計(jì)值上式中,ak∈r(m-1)×d為混合矩陣a中去除第k行所得到的矩陣。(4)計(jì)算實(shí)際值s與估計(jì)值之間的誤差并計(jì)算矩陣fk的協(xié)方差矩陣ck=fktfk/(n-1)。(5)計(jì)算矩陣ck最大特征值所對(duì)應(yīng)的特征向量αk∈rd×1,并置(6)判斷k<m?若是,則置k=k+1后返回步驟(3);若否,則執(zhí)行步驟(7)。(7)調(diào)用模型參數(shù)集實(shí)施在線過程監(jiān)測,具體的實(shí)施過程如下所示:①采集生產(chǎn)過程對(duì)象最新時(shí)刻的采樣數(shù)據(jù)ynew∈r1×m,對(duì)其進(jìn)行與x同樣的標(biāo)準(zhǔn)化處理得到②計(jì)算樣本向量所對(duì)應(yīng)的獨(dú)立成分向量的實(shí)際值并初始化k=1。③假設(shè)樣本向量中第k個(gè)變量數(shù)據(jù)缺失,將中其余數(shù)據(jù)組成新向量并利用公式計(jì)算得到獨(dú)立成分向量的估計(jì)值④計(jì)算獨(dú)立成分向量的實(shí)際值與估計(jì)值之間的誤差⑤按照如下所示公式計(jì)算監(jiān)測統(tǒng)計(jì)量qk:qk=(fkαk)2(1)⑦判斷k<m?若是,則置k=k+1后返回步驟③;若否,則執(zhí)行步驟⑧。⑧置q=max{q1,q2,…,qm}后,判斷是否滿足條件:若是,則當(dāng)前樣本是正常樣本,生產(chǎn)過程處于正常工作狀態(tài)并返回①繼續(xù)監(jiān)測下一個(gè)新樣本;若否,則該樣本為故障樣本,生產(chǎn)過程進(jìn)入非正常工況并觸發(fā)故障警報(bào)。其中,符號(hào)max{}表示取最大值,表示自由度為1、置信度為δ的卡方分布所對(duì)應(yīng)的數(shù)值。與傳統(tǒng)方法相比,本發(fā)明方法的優(yōu)勢主要體現(xiàn)在以下兩個(gè)方面:一方面,本發(fā)明方法監(jiān)測的對(duì)象是獨(dú)立成分的估計(jì)誤差,雖然獨(dú)立成分是非高斯分布的但誤差本身一般服從高斯分布??梢哉f,本發(fā)明方法是通過缺失變量的建模思路將非高斯過程采樣數(shù)據(jù)巧妙的轉(zhuǎn)換成了高斯分布的誤差數(shù)據(jù),對(duì)應(yīng)確定的控制限也就能對(duì)正常數(shù)據(jù)進(jìn)行更精確的描述。另一方面,本發(fā)明方法通過逐一假設(shè)各個(gè)測量變量數(shù)據(jù)缺失,從而建立了與監(jiān)測變量個(gè)數(shù)相等的故障檢測模型。與傳統(tǒng)基于單個(gè)ica模型的故障檢測方法相比,本發(fā)明方法還發(fā)揮了多模型泛化能力強(qiáng)的優(yōu)勢。綜合以上兩方面優(yōu)點(diǎn),本發(fā)明方法是一種更為優(yōu)選的非高斯過程監(jiān)測方法。附圖說明圖1為本發(fā)明方法的實(shí)施流程圖。圖2為誤差f1中第一列與獨(dú)立成分s中第一列元素的高斯分布檢驗(yàn)圖。圖3為本發(fā)明方法與傳統(tǒng)ica方法平均故障漏報(bào)率對(duì)比圖。具體實(shí)施方式下面結(jié)合附圖對(duì)本發(fā)明方法進(jìn)行詳細(xì)的說明。如圖1所示,本發(fā)明涉及一種基于缺失變量建模思路的非高斯過程監(jiān)測方法,該方法的具體實(shí)施步驟如下所示:(1)利用采樣系統(tǒng)收集生產(chǎn)過程正常運(yùn)行狀態(tài)下的樣本數(shù)據(jù),組成訓(xùn)練數(shù)據(jù)矩陣:x∈rn×m,并對(duì)x進(jìn)行標(biāo)準(zhǔn)化處理,使每個(gè)測量變量的均值為0,方差為1,得到新的數(shù)據(jù)矩陣其中,n為訓(xùn)練樣本數(shù),m為過程測量變量數(shù),r為實(shí)數(shù)集,rn×m表示n×m維的實(shí)數(shù)矩陣,為矩陣中第k個(gè)變量的n個(gè)測量數(shù)據(jù),k=1,2,…,m。(2)利用ica算法為建立ica模型,并初始化k=1。建立ica模型的的實(shí)施過程如下所示:①計(jì)算的協(xié)方差矩陣其中c∈rm×m;②計(jì)算矩陣c的所有特征值和特征向量,并剔除小于0.0001的特征值及其對(duì)應(yīng)的特征向量,得到特征向量矩陣p=[p1,p2,…,pm]∈rm×m以及特征值對(duì)角矩陣d=diag(λ1,λ2,…,λm)∈rm×m;值得注意的是,這里求解得到的特征向量p1,p2,…,pm都必須是單位長度的向量。③根據(jù)公式對(duì)進(jìn)行白化處理,得到z∈rn×m,并初始化i=1;④取列向量ci為m×m維單位矩陣中的第i列,⑤按照如下所示公式更新ci,即:ci←e{zg(citz)}-e{h(citz)}ci(2)上式(2)中,e{}表示求取期望值(即向量的平均值),函數(shù)g和h的具體形式如下所示:g(u)=tanh(u)(3)h(u)=[sech(u)]2(4)上式(3)與(4)中,u為函數(shù)自變量,在這里指代citz中的元素。⑥對(duì)更新后的向量ci依次按照下式進(jìn)行正交標(biāo)準(zhǔn)化處理:ci←ci/||ci||(6)⑦重復(fù)步驟⑤~⑥直至向量ci收斂,并保存向量ci;⑧判斷i<m?若是,置i=i+1后,重復(fù)步驟④~⑧;若否,執(zhí)行步驟⑨;⑨將得到的所有m個(gè)向量c1,c2,…,cm組成矩陣c=[c1,c2,…,cm]∈rm×m,并按照如下所示公式計(jì)算分離矩陣w0∈rm×m與混合矩陣a0∈rm×m:a0=pd1/2c(7)w0=pd-1/2c(8)⑩計(jì)算a0中每一列向量的長度,分別記為l1,l2,…,lm,并將l1,l2,…,lm按照數(shù)值大小進(jìn)行降序排列得到l1,l2,…,lm,那么保留的獨(dú)立成分個(gè)數(shù)d為滿足下列條件的最小值:將a0中列向量長度最大的d個(gè)列向量組成新的混合矩陣a∈rm×d,同時(shí)從w0中取出與a對(duì)應(yīng)的列向量組成新分離矩陣w∈rm×d;最后得到的ica模型為其中,為d個(gè)獨(dú)立成分列向量組成的矩陣,e∈rn×m表示模型誤差。(3)假設(shè)矩陣中第k列數(shù)據(jù)缺失,其余可用列組成矩陣xk∈rn×(m-1),并利用如下所示公式計(jì)算得到獨(dú)立成分矩陣的估計(jì)值上式中,ak∈r(m-1)×d為混合矩陣a中去除第k行所得到的矩陣。(4)計(jì)算實(shí)際值s與估計(jì)值之間的誤差并計(jì)算矩陣fk的協(xié)方差矩陣ck=fktfk/(n-1)。(5)計(jì)算矩陣ck最大特征值所對(duì)應(yīng)的特征向量αk∈rd×1,并置(6)判斷k<m?若是,則置k=k+1后返回步驟(3);若否,則執(zhí)行步驟(7)。(7)調(diào)用模型參數(shù)集實(shí)施在線過程監(jiān)測,具體的實(shí)施過程如下所示:①采集生產(chǎn)過程對(duì)象最新時(shí)刻的采樣數(shù)據(jù)ynew∈r1×m,對(duì)其進(jìn)行與x同樣的標(biāo)準(zhǔn)化處理得到②計(jì)算樣本向量所對(duì)應(yīng)的獨(dú)立成分向量的實(shí)際值并初始化k=1。③假設(shè)樣本向量中第k個(gè)變量數(shù)據(jù)缺失,將中其余數(shù)據(jù)組成新向量并利用公式計(jì)算得到獨(dú)立成分向量的估計(jì)值④計(jì)算獨(dú)立成分向量的實(shí)際值與估計(jì)值之間的誤差⑤按照如下所示公式計(jì)算監(jiān)測統(tǒng)計(jì)量qk:qk=(fkαk)2(11)⑦判斷k<m?若是,則置k=k+1后返回步驟③;若否,則執(zhí)行步驟⑧。⑧置q=max{q1,q2,…,qm}后,判斷是否滿足條件:若是,則當(dāng)前樣本是正常樣本,生產(chǎn)過程處于正常工作狀態(tài)并返回①繼續(xù)監(jiān)測下一個(gè)新樣本;若否,則該樣本為故障樣本,生產(chǎn)過程進(jìn)入非正常工況并觸發(fā)故障警報(bào)。其中,符號(hào)max{}表示取最大值,表示自由度為1、置信度為δ的卡方分布所對(duì)應(yīng)的數(shù)值。下面結(jié)合一個(gè)具體的工業(yè)過程的例子來說明本發(fā)明方法相對(duì)于現(xiàn)有方法的優(yōu)越性與可靠性。該過程數(shù)據(jù)來自于美國田納西-伊斯曼(te)化工過程實(shí)驗(yàn),原型是伊斯曼化工生產(chǎn)車間的一個(gè)實(shí)際工藝流程。目前,te過程因其流程的復(fù)雜性,已作為一個(gè)標(biāo)準(zhǔn)實(shí)驗(yàn)平臺(tái)被廣泛用于故障檢測研究。整個(gè)te過程包括22個(gè)測量變量、12個(gè)操作變量、和19個(gè)成分測量變量。所采集的數(shù)據(jù)分為22組,其中包括1組正常工況下的數(shù)據(jù)集與21組故障數(shù)據(jù)。而在這些故障數(shù)據(jù)中,有16個(gè)是已知故障類型,如冷卻水入口溫度或進(jìn)料成分的變化、閥門粘滯、反應(yīng)動(dòng)力學(xué)漂移等,還有5個(gè)故障類型是未知的。為了對(duì)該過程進(jìn)行監(jiān)測,選取如表1所示的33個(gè)過程變量,接下來結(jié)合該te過程對(duì)本發(fā)明具體實(shí)施步驟進(jìn)行詳細(xì)的闡述。表1:te過程監(jiān)測變量。序號(hào)變量描述序號(hào)變量描述序號(hào)變量描述1物料a流量12分離器液位23d進(jìn)料閥門位置2物料d流量13分離器壓力24e進(jìn)料閥門位置3物料e流量14分離器塔底流量25a進(jìn)料閥門位置4總進(jìn)料流量15汽提塔等級(jí)26a和c進(jìn)料閥門位置5循環(huán)流量16汽提塔壓力27壓縮機(jī)循環(huán)閥門位置6反應(yīng)器進(jìn)料17汽提塔底部流量28排空閥門位置7反應(yīng)器壓力18汽提塔溫度29分離器液相閥門位置8反應(yīng)器等級(jí)19汽提塔上部蒸汽30汽提塔液相閥門位置9反應(yīng)器溫度20壓縮機(jī)功率31汽提塔蒸汽閥門位置10排空速率21反應(yīng)器冷卻水出口溫度32反應(yīng)器冷凝水流量11分離器溫度22分離器冷卻水出口溫度33冷凝器冷卻水流量(1)采集te過程對(duì)象正常工況下的過程數(shù)據(jù),并選取960個(gè)正常數(shù)據(jù)組成矩陣x∈r960×33,對(duì)其進(jìn)行標(biāo)準(zhǔn)化處理得到(2)利用ica算法為建立ica模型,即:并初始化k=1。(3)假設(shè)矩陣中第k列數(shù)據(jù)缺失,其余可用列組成矩陣xk∈r960×32,并利用如下所示公式計(jì)算得到獨(dú)立成分矩陣的估計(jì)值上式中,ak∈r32×28為混合矩陣a中去除第k行所得到的矩陣;(4)計(jì)算實(shí)際值s與估計(jì)值之間的誤差并計(jì)算矩陣fk的協(xié)方差矩陣ck=fktfk/(n-1);由于本發(fā)明方法監(jiān)測的對(duì)象為誤差fk,而傳統(tǒng)ica方法監(jiān)測的是獨(dú)立成分s,特對(duì)f1中第一列與獨(dú)立成分矩陣s中第一列的數(shù)據(jù)進(jìn)行高斯分布檢驗(yàn),結(jié)果顯示于圖2中。若所測試數(shù)據(jù)嚴(yán)格服從高斯分布,圖2中的散點(diǎn)圖則為一條直線。很顯然,本發(fā)明方法中誤差f1近似服從高斯分布,而傳統(tǒng)ica方法中由于提取的是非高斯的獨(dú)立成分,當(dāng)然就不符合高斯分布。從這個(gè)對(duì)比也可以說明,本發(fā)明方法可以將非高斯的成分巧妙地轉(zhuǎn)換成近似服從高斯分布的誤差。這樣一來,本發(fā)明方法確定的控制限就可以按照卡方分布分來獲取。(5)計(jì)算矩陣ck最大特征值所對(duì)應(yīng)的特征向量αk∈r28×1,并置(6)判斷k<m?若是,則置k=k+1后返回步驟(3);若否,則離線建模完成并實(shí)施在線故障監(jiān)測;為測試本發(fā)明方法的在故障檢測上的優(yōu)越性,以監(jiān)測te過程21種故障的平均故障檢測成功率為例,對(duì)比本發(fā)明方法與傳統(tǒng)基于ica方法的故障檢測效果。該測試數(shù)據(jù)有960個(gè)樣本組成,其前160個(gè)樣本為正常工況下采樣,后800個(gè)樣本為故障工況采樣。①采集生產(chǎn)過程對(duì)象最新時(shí)刻的采樣數(shù)據(jù)ynew∈r1×33,對(duì)其進(jìn)行與x同樣的標(biāo)準(zhǔn)化處理得到②計(jì)算樣本向量所對(duì)應(yīng)的獨(dú)立成分向量的實(shí)際值并初始化k=1;③假設(shè)樣本向量中第k個(gè)變量數(shù)據(jù)缺失,將中其余數(shù)據(jù)組成新向量并利用公式計(jì)算得到獨(dú)立成分向量的估計(jì)值④計(jì)算獨(dú)立成分向量的實(shí)際值與估計(jì)值之間的誤差⑤按照如下所示公式計(jì)算監(jiān)測統(tǒng)計(jì)量qk:qk=(fkαk)2(2)⑦判斷k<33?若是,則置k=k+1后返回步驟③;若否,則執(zhí)行步驟⑧;⑧置q=max{q1,q2,…,q33}后,根據(jù)條件決策故障是否發(fā)生。本發(fā)明發(fā)與傳統(tǒng)ica方法針對(duì)te過程21種故障類型的平均故障漏報(bào)率顯示于圖3中,可以發(fā)現(xiàn),本發(fā)明方法的平均故障漏報(bào)率明顯低于傳統(tǒng)ica方法。因此,本發(fā)明方法改進(jìn)了基于ica的非高斯過程監(jiān)測方法的故障檢測性能。上述實(shí)施例只用來解釋本發(fā)明,而不是對(duì)本發(fā)明進(jìn)行限制,在本發(fā)明的精神和權(quán)利要求的保護(hù)范圍內(nèi),對(duì)本發(fā)明做出的任何修改和改變,都落入本發(fā)明的保護(hù)范圍內(nèi)。當(dāng)前第1頁12