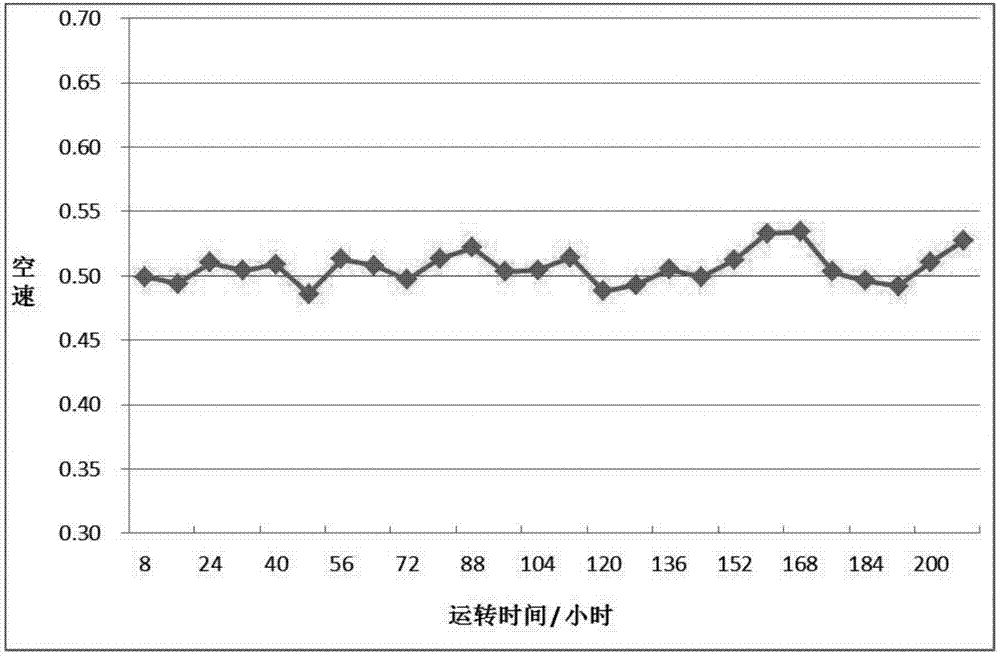
本發(fā)明屬于輪胎裂解油的加工處理
技術(shù)領(lǐng)域:
,特指一種廢舊輪胎裂解汽柴蠟油混合餾分的加氫改質(zhì)方法。
背景技術(shù):
:伴隨著我國汽車保有量的不斷攀升,廢舊輪胎的產(chǎn)生量也隨之快速增長,按照目前廢舊輪胎增長速度,在2020年廢舊輪胎的產(chǎn)生量估計將達到2000萬噸。然而現(xiàn)在我國廢輪胎的有效利用率卻不到50%,因此,提高廢舊輪胎的回收利用率空間很大。其中輪胎裂解技術(shù)作為廢舊輪胎回收利用最好的方法之一,其研究和應用發(fā)展迅速。裂解油是廢舊輪胎裂解過程的主要產(chǎn)物,其質(zhì)量直接影響著裂解過程的經(jīng)濟可行性和發(fā)展前景。廢輪胎裂解油的熱值較高,但如果直接作為燃料油使用經(jīng)濟價值不大,而且由于其中硫、氮含量高,直接使用會造成嚴重的環(huán)境污染。因此,對裂解油品進行進一步加氫精制脫硫脫氮等產(chǎn)出石腦油、柴油和重油組分不僅可以使產(chǎn)品的應用更加環(huán)保,更可以將非標的裂解油品生產(chǎn)為國標的汽柴油組分,從而大大提升產(chǎn)品的附加值?,F(xiàn)行的輪胎裂解技術(shù)通常是將廢輪胎裂解油首先進行蒸餾,分餾為汽油餾分、柴油餾分以及重油組分,然后分別針對不同餾分進行加氫處理,這樣固然可以更好的針對不同餾分的特點設計差異化的加氫處理方案,但是這樣也造成了該反應工藝流程復雜,所需設備投資較大,不適合小型化生產(chǎn)。輪胎裂解油與原油相比,許多指標都較優(yōu)。裂解油品的蠟含量、凝點比一般原油低,芳烴含量較高,烷烴和瀝青質(zhì)含量低,低沸點物質(zhì)較多,閃點低,灰分、殘?zhí)?、固體雜質(zhì)含量均很少。裂解油中的微量金屬元素含量均比原油低,對后期加氫精制催化劑的使用不造成影響。因此可以對輪胎裂解油直接進行加氫改質(zhì)處理,這需要一種滿足輪胎裂解油混合餾分為原料的催化工藝和操作條件,實現(xiàn)廢輪胎裂解油一步加氫生成優(yōu)質(zhì)燃料油過程,從而節(jié)約投資成本。技術(shù)實現(xiàn)要素:本發(fā)明的目的是提供工藝簡單的一種廢舊輪胎裂解汽柴蠟油混合餾分的加氫改質(zhì)方法。本發(fā)明的目的是這樣實現(xiàn)的:一種廢舊輪胎裂解汽柴蠟油混合餾分的加氫改質(zhì)方法,其特征在于:包括由第一、第二、第三反應器串聯(lián)而成的用于原料油的改質(zhì)的反應裝置,第一反應器、第二反應器和第三反應器中具體的填裝方案如下:第一反應器中的反應管的入口至出口依次填裝保護劑40c、保護劑40d和磁球,并將反應管的入口與第一反應器中的入口管路連接;第二反應器中的反應管的入口至出口依次填裝磁球、精制催化劑lb207k和磁球,并將反應管的入口與第二反應器中的入口管路連接;第三反應器中的反應管的入口至出口依次填裝磁球、精制催化劑lb207k和磁球,并將反應管的入口與第三反應器中的入口管路連接;其工藝流程步驟如下:(1)將原料油通過進料泵升壓至12-18mpa后注入待反應容器中;(2)將氫氣經(jīng)壓縮機升壓至15mpa,然后將升壓后的氫氣注入待反應容器中的與升壓后的原料油混合,體積空速為0.3-1.0h-1,氫氣與原料油的體積比為600-1200nm3/m3;(3)打開氮氣進氣閥將氮氣通入第一、第二、第三反應器中,在通入氮氣的同時將第一反應器的溫度加熱至210-320℃、第二反應器的溫度加熱至300-420℃、第三反應器的溫度加熱至300-420℃;(4)將步驟(3)持續(xù)至少1小時后,關(guān)閉氮氣進氣閥,打開待反應容器中的球閥,將步驟(2)中混合的原料油通過入口管路進入反應器開始反應;上述原料油為輪胎裂解油的汽油、柴油和蠟油混合餾分,汽油、柴油和蠟油的質(zhì)量比為1:(1.2-3.5):(1.2-3.5)。上述原料油為輪胎裂解油的汽油、柴油和蠟油混合餾分,汽油、柴油和蠟油的質(zhì)量比為1:2:1.8時:步驟(1)中原料油通過進料泵升壓至15mp,原料油注入待反應容器中的進樣量約為0.275kg/h;步驟(2)中的氫氣與原料油的體積比為1000nm3/m3;步驟(3)中的第一反應器的溫度為250℃,第二反應器的溫度為360℃,第三反應器的溫度為360℃。上述第一反應器中的反應管的入口至出口依次填裝的保護劑40c的填裝體積為200ml,保護劑40d的填裝體積為200ml,磁球的填裝體積為80ml。所述第二反應器中的反應管的入口至出口依次填裝的磁球的填裝體積為130ml,精制催化劑lb207k的填裝體積為300ml,磁球的填裝體積為80ml。所述第三反應器中的反應管的入口至出口依次填裝的磁球的填裝體積為140ml,精制催化劑lb207k的填裝體積為300ml,磁球的填裝體積為80ml。上述第一、第二、第三反應器內(nèi)徑為26mm,高度1380mm,熱電偶套管外徑9.5mm,反應器平均截面積為381.5mm2。上述第一、第二、第三反應器均由設置在加熱器中5片爐瓦連續(xù)加熱,每片爐瓦高23cm,合計高115cm,反應器入口距離第一片爐瓦10cm,第五片爐瓦距反應器出口13cm。上述保護劑40c和保護劑40d均為氧化鋁負載鎳鉬組分的物質(zhì),保護劑40c的比表面積和孔徑均大于保護劑40d的比表面積和孔徑;所述精制催化劑lb207k為:氧化鋁負載鈷鉬組分的催化劑,精制催化劑lb207k中mo含量達到10-25w%,mo/co比值達到2-8。本發(fā)明相比現(xiàn)有技術(shù)突出且有益的技術(shù)效果是:本發(fā)明作為一種較簡單的輪胎裂解油加氫改質(zhì)方法具有工藝簡單,投資少,所改質(zhì)后的裂解油不同餾分產(chǎn)物的各個指標得到明顯改善,顯著提高了輪胎裂解油的經(jīng)濟價值。附圖說明圖1是本發(fā)明催化劑在各個反應器中的添加方案圖。圖2是本發(fā)明加氫過程中空速隨運轉(zhuǎn)時間的波動變化圖。圖3是本發(fā)明加氫過程中全餾分油的密度隨運轉(zhuǎn)時間的變化圖。具體實施方式下面結(jié)合附圖以具體實施例對本發(fā)明作進一步描述,參見圖1—3:一種廢舊輪胎裂解汽柴蠟油混合餾分的加氫改質(zhì)方法,包括由第一、第二、第三反應器串聯(lián)而成的用于原料油的改質(zhì)的反應裝置,原料油為輪胎裂解油的汽油、柴油和蠟油混合餾分,汽油、柴油和蠟油的質(zhì)量比為1:(1.2-3.5):(1.2-3.5),優(yōu)選的,本發(fā)明原料油中的汽油、柴油和蠟油的質(zhì)量比為1:2:1.8。第一、第二、第三反應器的內(nèi)徑為26mm,高度1380mm,熱電偶套管外徑9.5mm,反應器平均截面積為381.5mm2,第一、第二、第三反應器均由設置在加熱器中5片爐瓦連續(xù)加熱,每片爐瓦高23cm,合計高115cm,反應器入口距離第一片爐瓦10cm,第五片爐瓦距反應器出口13cm。第一反應器、第二反應器和第三反應器中具體的填裝方案如下:第一反應器中的反應管的入口至出口依次填裝保護劑40c、保護劑40d和磁球,反應管的入口至出口依次填裝的保護劑40c的填裝體積為200ml,保護劑40d的填裝體積為200ml,磁球的填裝體積為80ml;填裝過程量保證填入物堆積均勻,防止填入的固體超過反應器的總高度,填裝完畢后,將反應管的入口與第一反應器中的入口管路連接;第二反應器中的反應管的入口至出口依次填裝磁球、精制催化劑lb207k和磁球,反應管的入口至出口依次填裝的磁球的填裝體積為130ml,精制催化劑lb207k的填裝體積為300ml,磁球的填裝體積為80ml;填裝過程量保證填入物堆積均勻,防止填入的固體超過反應器的總高度,填裝完畢后,并將反應管的入口與第二反應器中的入口管路連接;第三反應器中的反應管的入口至出口依次填裝磁球、精制催化劑lb207k和磁球,反應管的入口至出口依次填裝的磁球的填裝體積為140ml,精制催化劑lb207k的填裝體積為300ml,磁球的填裝體積為80ml;填裝過程量保證填入物堆積均勻,防止填入的固體超過反應器的總高度,填裝完畢后,并將反應管的入口與第三反應器中的入口管路連接;其工藝流程步驟如下:(1)將原料油通過進料泵升壓至12-18mpa后注入待反應容器中,優(yōu)選的本發(fā)明將原料油升壓至15mpa,原料油注入待反應容器中的進樣量約為0.275kg/h;(2)將氫氣經(jīng)壓縮機升壓至15mpa,然后將升壓后的氫氣注入待反應容器中的與升壓后的原料油混合,氫氣與原料油的體積比為600-1200nm3/m3;優(yōu)選的本發(fā)明的氫氣與原料油的體積比為1000nm3/m3。(3)打開氮氣進氣閥將氮氣通入第一、第二、第三反應器中,在通入氮氣的同時將第一反應器的溫度加熱至210-320℃、第二反應器的溫度加熱至300-420℃、第三反應器的溫度加熱至300-420℃;優(yōu)選的本發(fā)明將第一反應器的溫度加熱至250℃、第二反應器的溫度加熱至360℃、第三反應器的溫度加熱至360℃;(4)將步驟(3)持續(xù)至少1小時后,關(guān)閉氮氣進氣閥,打開待反應容器中的球閥,將步驟(2)中混合的原料油通過入口管路進入反應器開始反應;反應總共進行208小時,反應開始后每隔8h收集一次液體和氣體產(chǎn)物進行分析。上述保護劑40c和保護劑40d均為氧化鋁負載鎳鉬組分的物質(zhì),主要是預處理和保護精制催化劑的作用,其中保護劑40c的比表面積和孔徑均大于保護劑40d的比表面積和孔徑,有助于反應分子的擴散,而且經(jīng)過了一定的預硫化,初活性較高;保護劑的作用主要有:脫除或攔截原料油中的顆粒物、垢物、結(jié)焦、金屬雜質(zhì)等,保護主催化劑及延長主催化劑的使用壽命,防止反應器床層壓力降的快速升高,延長裝置的運轉(zhuǎn)周期。上述精制催化劑lb207k為:氧化鋁負載鈷鉬組分的催化劑,精制催化劑lb207k中mo含量達到10-25w%,mo/co比值達到2-8。本發(fā)明中原料油的組成性質(zhì)見下表。保護劑40c和40d、精制催化劑lb207k均由催化劑廠家購買。本發(fā)明輪胎裂解油原料加氫改質(zhì)的操作條件如表1所示:表1不同輪胎裂解油原料加氫精制的操作反應條件運作時間/h208操作壓力/mpa15.0氫油體積比/nm3/m31000體積空速為/h-10.5反應器一的平均溫度/℃250反應器二的平均溫度/℃360反應器三的平均溫度/℃360進一步對輪胎裂解油加氫改質(zhì)產(chǎn)物進行物料平衡計算以及產(chǎn)物組成與性質(zhì)的分析,從而評價本發(fā)明加氫改質(zhì)催化工藝的效果。首先輪胎裂解油加氫改質(zhì)整體的催化工藝過程物料平衡如表2所示。從表2中可以看出,經(jīng)過加氫改質(zhì)催化過程,因脫除了輪胎裂解油中的大部分的s、n等元素而產(chǎn)生了大量的h2s、nh3。此外產(chǎn)生了少量烴類氣體產(chǎn)物,其具體分子組成如表2所示。氣體產(chǎn)物除了含有相對較多的甲烷、乙烷以外,其余氣體產(chǎn)物主要集中在丁烯和c5+分布最多,合計達到氣體產(chǎn)物中的65w%以上。原料油經(jīng)加氫改質(zhì)后的液體產(chǎn)物中各餾分比例發(fā)生了明顯的變化,其中柴油餾分明顯增多,達到了68.04%,而蠟油餾分明顯減少,整體汽柴蠟油比例由原來的1:2:1.8變?yōu)榧s1:3.5:0.4。這說明在加氫改質(zhì)過程中,蠟油餾分發(fā)生了催化裂化反應,使得部分蠟油轉(zhuǎn)化成了產(chǎn)物中柴油餾分。表2輪胎裂解油加氫改質(zhì)物料平衡表3加氫精制氣體產(chǎn)物組成產(chǎn)物占比/w%甲烷8.64乙烷13.8乙烯3.19丙烷2.68丙烯1.95異丁烷2.04正丁烷2.69丁烯24.72c5+40.29合計100對輪胎裂解油加氫改質(zhì)的全餾分液體產(chǎn)物的組成與性質(zhì)進行分析,其結(jié)果如表4所示。由表4可知,經(jīng)過加氫改質(zhì)后,液體產(chǎn)物的密度、粘度、殘?zhí)康戎笜嗣黠@變小,而液體產(chǎn)物的h/c原子比明顯提高,說明輪胎裂解油加氫改質(zhì)效果顯著。表4全餾分液體產(chǎn)物的性質(zhì)為了分別對比液體產(chǎn)物不同餾分性質(zhì)的變化,進一步對加氫改質(zhì)液體產(chǎn)物的石腦油餾分(ibp~180℃)、柴油餾分(180~360℃)、減壓餾分油(>360℃)三種不同餾分油分別進行分析,其結(jié)果如表5-7所示。由表5中各項指標可知,石腦油餾分中芳香烴含量明顯減少,而鏈烷烴含量明顯得到提高,s、n含量等各項指標達到了較高的水平。加氫改質(zhì)后的柴油餾分性質(zhì)如表6所示,絕大數(shù)指標已經(jīng)達到國標輕柴油(gb252-2000)的質(zhì)量要求,特別是硫含量、酸度等指標達到了較高的水平。從表7中可以看出,減壓餾分油的酸度、硫氮含量等指標與汽柴油餾分相比達到了更高的水平。表5加氫石腦油(ibp~180℃)性質(zhì)與組成表6加氫柴油餾分(180~360℃)性質(zhì)與組成表7加氫減壓餾分油(>360℃)性質(zhì)與組成上述實施例僅為本發(fā)明的較佳實施例,并非依此限制本發(fā)明的保護范圍,故:凡依本發(fā)明的結(jié)構(gòu)、形狀、原理所做的等效變化,均應涵蓋于本發(fā)明的保護范圍之內(nèi)。當前第1頁12