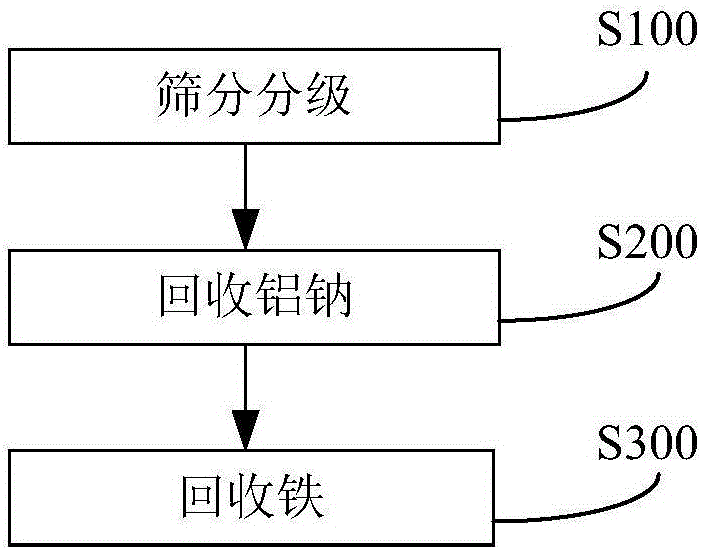
本實用新型屬于能源與冶金領(lǐng)域,具體而言,本實用新型涉及處理赤泥的系統(tǒng)。
背景技術(shù):
:赤泥,是鋁土礦提煉氧化鋁過程中產(chǎn)生的廢棄物,因其為赤紅色泥漿而得名。隨著鋁工業(yè)的不斷發(fā)展,目前全世界每年產(chǎn)出約6000萬噸赤泥,我國的赤泥排放量每年為450萬噸以上。世界上大多數(shù)氧化鋁廠是將赤泥堆積或者傾入深海。赤泥中含有大量的鐵、鋁、鈉、鈣等金屬,赤泥的堆存不僅占用大量的土地和農(nóng)田,耗費較多的堆場建設(shè)及維護費用,造成嚴重的水質(zhì)污染,且浪費了大量的金屬資源。赤泥中所含有價金屬組分如Fe3O4、Al2O3、Na2O、TiO2,多為經(jīng)濟價值較低的賤金屬,單獨就某一種元素進行回收利用不能很好的解決工藝經(jīng)濟性和赤泥堆存量巨大的問題,必須采用多種金屬聯(lián)合回收技術(shù)才能真正的實現(xiàn)赤泥的綜合利用和減量化。因此,赤泥的綜合治理及其金屬資源的有效回收成為人們?nèi)找骊P(guān)注的焦點。赤泥的處理主要還是外排前采用強磁選,提取部分鐵精礦,尾礦直接堆存。技術(shù)實現(xiàn)要素:本實用新型旨在至少在一定程度上解決相關(guān)技術(shù)中的技術(shù)問題之一。為此,本實用新型的一個目的在于提出一種具有高效回收鋁、鈉和鐵的處理赤泥的系統(tǒng)。根據(jù)本實用新型的一個方面,本實用新型還提出了一種處理赤泥的系統(tǒng),該系統(tǒng)包括:第一篩分裝置,所述第一篩分裝置具有赤泥入口、第一篩上赤泥出口和第一篩下赤泥出口,所述第一篩分裝置內(nèi)的篩子的孔徑為1.0mm,其中,所述第一篩上赤泥出口適于排出第一赤泥;第二篩分裝置,所述第二篩分裝置具有第一篩下赤泥入口、第二篩上赤泥出口和第二篩下赤泥出口,所述第一篩下赤泥入口與所述第一篩下赤泥出口相連,所述第二篩分裝置內(nèi)的篩子的孔徑為0.074mm,其中,所述第二篩上赤泥出口適于排出第二赤泥,所述第二篩下赤泥出口適于排出第三赤泥;混合裝置,所述混合裝置具有第一赤泥入口、第三赤泥入口、添加劑入口和混合物料出口,所述第一赤泥入口與所述第一篩上赤泥出口相連、所述第三赤泥入口與所述第二篩下赤泥出口相連;第一焙燒裝置,所述第一焙燒裝置具有混合物料入口和焙燒產(chǎn)物出口,所述混合物料入口與所述混合物料出口相連;浸出裝置,所述浸出裝置具有堿液入口、焙燒產(chǎn)物入口、浸出液出口和浸出渣出口,所述焙燒產(chǎn)物入口與焙燒產(chǎn)物出口相連;混合成型裝置,所述混合成型裝置具有第二赤泥入口、浸出渣入口、還原劑入口和物料球團出口,所述第二赤泥入口與所述第二篩上赤泥出口相連,所述浸出渣入口與所述浸出渣出口相連;以及第二焙燒裝置,所述第二焙燒裝置具有物料球團入口和金屬化球團出口,所述物料球團入口與所述物料球團出口相連。本實用新型上述實施例的處理赤泥的系統(tǒng)將赤泥進行分級處理,將赤泥中含有的大量的鈉和鋁集中在粒徑<0.074mm的赤泥中,先將鋁和鈉進行回收,得到的浸出渣再與含少量鋁和鈉元素的赤泥混合提取鐵。由于堿金屬減少,不但可以提高混合赤泥的鐵品位和鐵的回收率,同時還可以減輕堿金屬對第二焙燒裝置中耐火材料的侵蝕。因此,采用本實用新型上述實施例的處理赤泥的系統(tǒng)可以高效回收赤泥中的鋁、鈉和鐵,達到對赤泥中的有價金屬進行分步高效回收。在本實用新型中,所述添加劑入口包括碳酸鈉入口和氧化鈣入口。附圖說明圖1是根據(jù)本實用新型一個實施例的處理赤泥的系統(tǒng)的結(jié)構(gòu)示意圖。圖2是根據(jù)本實用新型一個實施例的處理赤泥的方法的流程圖。圖3是根據(jù)本實用新型另一個實施例的處理赤泥的方法的流程圖。具體實施方式下面詳細描述本實用新型的實施例,所述實施例的示例在附圖中示出,其中自始至終相同或類似的標號表示相同或類似的元件或具有相同或類似功能的元件。下面通過參考附圖描述的實施例是示例性的,旨在用于解釋本實用新型,而不能理解為對本實用新型的限制。根據(jù)本實用新型的一個方面,本實用新型提出了一種處理赤泥的系統(tǒng)。下面參考圖1詳細描述本實用新型具體實施例的處理赤泥的系統(tǒng)。根據(jù)本實用新型具體實施例的處理赤泥的系統(tǒng)包括:第一篩分裝置10、第二篩分裝置20、混合裝置30、第一焙燒裝置40、浸出裝置50、混合成型裝置60和第二焙燒裝置70。其中,第一篩分裝置10具有赤泥入口11、第一篩上赤泥出口12和第一篩下赤泥出口13,第一篩分裝置10內(nèi)的篩子的孔徑為1.0mm,其中,第一篩上赤泥出口12適于排出粒徑≥1.0mm的第一赤泥;第二篩分裝置20具有第一篩下赤泥入口21、第二篩上赤泥出口22和第二篩下赤泥出口23,第一篩下赤泥入口21與第一篩下赤泥出口13相連,第二篩分裝置20內(nèi)的篩子的孔徑為0.074mm,其中,第二篩上赤泥出口22適于排出粒徑<1.0mm且≥0.074mm的第二赤泥,第二篩下赤泥出口23適于排出粒徑<0.074mm的第三赤泥;混合裝置30具有第一赤泥入口31、第三赤泥入口32、添加劑入口33和混合物料出口34,第一赤泥入口31與第一篩上赤泥出口12相連、第三赤泥入口32與第二篩下赤泥出口23相連;第一焙燒裝置40具有混合物料入口41和焙燒產(chǎn)物出口42,混合物料入口41與混合物料出口34相連;浸出裝置50,浸出裝置具有堿液入口51、焙燒產(chǎn)物入口52、浸出液出口53和浸出渣出口54,焙燒產(chǎn)物入口52與焙燒產(chǎn)物出口42相連;混合成型裝置60具有第二赤泥入口61、浸出渣入口62、還原劑入口63和物料球團出口64,第二赤泥入口61與第二篩上赤泥出口22相連,浸出渣入口62與浸出渣出口54相連;以及第二焙燒裝置70具有物料球團入口71和金屬化球團出口72,物料球團入口71與物料球團出口64相連。根據(jù)本實用新型的具體實施例,利用上述實施例的處理赤泥的系統(tǒng)對赤泥進行處理,具體可以按照下列步驟進行:首先,利用第一篩分裝置10對赤泥進行第一篩分處理,得到粒徑≥1.0mm的第一赤泥,利用第二篩分裝置20對第一篩下赤泥進行第二篩分處理,得到粒徑<1.0mm且≥0.074mm的第二赤泥和粒徑<0.074mm的第三赤泥。由此將赤泥按照粒徑大小分為三部分。進一步地,在混合裝置30中,將粒徑≥1.0mm的第一赤泥和粒徑<0.074mm的第三赤泥混合并加入適量的添加劑進行混合,并進一步地將得到的混合物料在第一焙燒裝置40和浸出裝置50中進行第一焙燒和和浸出處理,進而浸出赤泥中的鋁。最后將浸出鋁后的浸出渣與粒徑<1.0mm且≥0.074mm的第二赤泥在混合成型裝置60中與適量的還原劑進行混合,并送入第二焙燒裝置70中進行第二焙燒處理,并得到金屬化球團。由此對赤泥中的金屬鐵進行回收。本實用新型上述實施例的處理赤泥的系統(tǒng)將赤泥進行分級處理,將赤泥中含有的大量的鈉和鋁集中在粒徑<0.074mm的赤泥中,先將鋁和鈉進行回收,得到的浸出渣再與含少量鋁和鈉元素的赤泥混合提取鐵。由于堿金屬減少,不但可以提高混合赤泥的鐵品位和鐵的回收率,同時還可以減輕堿金屬對第二焙燒裝置中耐火材料的侵蝕。因此,采用本實用新型上述實施例的處理赤泥的系統(tǒng)可以高效回收赤泥中的鋁、鈉和鐵,達到對赤泥中的有價金屬進行分步高效回收。實用新型人通過對赤泥進行分級,發(fā)現(xiàn),其中粒徑≥1.0mm的赤泥中氧化鈣占總赤泥氧化鈣量的60%,<0.074mm的赤泥Al2O3占總赤泥Al2O3量的90%,絕大部分的Al2O3富集在<0.074mm的赤泥中。為此,實用新型人設(shè)置第一篩分裝置10內(nèi)的篩子的孔徑為1.0mm,第二篩分裝置20內(nèi)的篩子的孔徑為0.074mm。從而預(yù)先對赤泥進行篩分處理,可以將赤泥中的鋁和鈉進行集中減量,進而便于后續(xù)的單獨分離,降低處理難度,提高回收鋁和鈉的效率。根據(jù)本實用新型的具體實施例,通過采用混合裝置30、第一焙燒裝置40和浸出裝置50,首先對粒徑≥1.0mm的第一赤泥、粒徑<0.074mm的第三赤泥和添加劑進行混合,并進行第一焙燒和浸出處理。由此,通過第一焙燒裝置40和浸出裝置50可以有效地回收赤泥中的鋁和鈉。根據(jù)本實用新型的具體實施例,添加劑入口包括碳酸鈉入口和氧化鈣入口。由于粒徑≥1.0mm的赤泥中的氧化鈣占總赤泥氧化鈣量的60%,因此將粒徑≥1.0mm的第一赤泥與粒徑<0.074mm的第三赤泥在混合裝置30內(nèi)混合,可以有效地利用赤泥中的大部分氧化鈣,進而可以節(jié)省添加劑的用量,降低成本。根據(jù)本實用新型的具體實施例,在第一焙燒裝置40內(nèi),碳酸鈉和氧化鈣的混合物與<0.074mm的赤泥混合后進行焙燒,碳酸鈉與赤泥中的Al2O3生成可以溶于堿液的Na2O·Al2O3,氧化鈣與赤泥中的SiO2生成2CaO·SiO2,防止SiO2與Al2O3生產(chǎn)Al2O3·SiO2,影響最終鋁的溶出。由此,通過上述焙燒處理,可以使得赤泥中的Al2O3生成可以溶于堿液的Na2O·Al2O3,進而便于后續(xù)鋁的浸出回收。根據(jù)本實用新型的具體實施了,添加劑中碳酸鈉的加入量可以按Na/Al=1.2-1.6(摩爾比)計算,氧化鈣加入量可以按Ca/Si=2.0-3.0(摩爾比)計算。由此可以加入適量的添加劑,避免浪費。根據(jù)本實用新型的具體實施例,第一焙燒裝置內(nèi)的溫度可以為800-1100攝氏度,第一焙燒時間可以為20-50分鐘。由此可以使得赤泥中的Al2O3與碳酸鈉充分反應(yīng),進而提高鋁的回收率。根據(jù)本實用新型的具體實施例,在浸出裝置50內(nèi),利用堿液對焙燒產(chǎn)物進行浸出處理,以便得到含有鋁酸鈉的浸出液和浸出渣。由此,通過堿液浸出,使得鋁和鈉進入到浸出液中,其余保留在浸出渣中。進一步地,可以從含有鋁酸鈉的浸出液中回收鋁。進而實現(xiàn)從赤泥中單獨回收鋁。根據(jù)本實用新型的具體實施例,對焙燒產(chǎn)物進行浸出處理采用的堿液中Na2Ok的濃度為10-20g/L,Na2OC的濃度為3-8g/L。由此可以進一步提高浸出效率,提高鋁回收率。根據(jù)本實用新型的具體實施例,通過采用混合成型裝置60和第二焙燒裝置70對回收鋁后的浸出渣與粒徑<1.0mm且≥0.074mm的第二赤泥和還原劑進行混合成型處理和第二焙燒處理,以便得到金屬化球團。根據(jù)本實用新型的具體實施例,第二焙燒裝置70內(nèi)的溫度為1200-1350攝氏度,第二焙燒時間為20-40分鐘。由此可以進一步提高焙燒效率,提高金屬鐵回收率。由此,將回收鋁后的浸出渣與含鋁量較少的粒徑<1.0mm且≥0.074mm的第二赤泥共同進行提鐵處理,可一步實現(xiàn)赤泥中金屬鐵的回收。由于預(yù)先對堿金屬進行單獨回收,不但可以提高混合赤泥的鐵品位和鐵的回收率,同時還可以減輕堿金屬對提鐵設(shè)備耐火材料的侵蝕。因此,本實用新型上述實施例的處理赤泥的系統(tǒng)可以高效回收赤泥中的鋁、鈉和鐵,達到對赤泥中的有價金屬進行分步高效回收利用。為了方便理解本實用新型上述實施例的處理赤泥的系統(tǒng),下面對采用該系統(tǒng)處理赤泥的方法進行描述。該方法包括:利用第一篩分裝置和第二篩分裝置將赤泥進行篩分處理,以便分別得到粒徑≥1.0mm的第一赤泥、粒徑<1.0mm且≥0.074mm的第二赤泥和粒徑<0.074mm的第三赤泥;利用混合裝置將第一赤泥、第三赤泥和添加劑進行混合,以便得到混合物料;利用第一焙燒裝置將混合物料進行第一焙燒處理,以便得到焙燒產(chǎn)物;在浸出裝置中利用堿液對焙燒產(chǎn)物進行浸出處理,以便得到含有鋁酸鈉的浸出液和浸出渣;利用混合成型裝置將第二赤泥與浸出渣和還原劑進行混合成型處理,以便得到物料球團;以及利用第二焙燒裝置將物料球團進行第二焙燒處理,以便得到金屬化球團。本實用新型上述實施例的處理赤泥的方法將赤泥進行分級處理,將赤泥中含有的大量的鈉和鋁集中在粒徑<0.074mm的赤泥中,先將鋁和鈉進行回收,得到的浸出渣再與含少量鋁和鈉元素的赤泥混合提取鐵。由于堿金屬減少,不但可以提高混合赤泥的鐵品位和鐵的回收率,同時還可以減輕堿金屬對提鐵設(shè)備耐火材料的侵蝕。因此,采用本實用新型上述實施例的處理赤泥的方法可以高效回收赤泥中的鋁、鈉和鐵,達到對赤泥中的有價金屬進行分步高效回收。下面參考圖2-3詳細描述利用本實用新型具體實施例的處理赤泥的系統(tǒng)對赤泥進行處理的方法。S100:篩分分級根據(jù)本實用新型的具體實施例,首先,利用第一篩分裝置和第二篩分裝置將赤泥進行篩分處理,以便分別得到粒徑≥1.0mm的第一赤泥、粒徑<1.0mm且≥0.074mm的第二赤泥和粒徑<0.074mm的第三赤泥。赤泥中含有少量的鋁和鈉,由于其難以單獨回收,因此,現(xiàn)有赤泥的處理工藝中,均放棄了鋁和鈉的回收。目前沒有一種成熟的方法能夠有效地單獨回收赤泥的中的鋁和鈉。實用新型人發(fā)現(xiàn),赤泥中的鈉和鋁大多集中粒徑較小的赤泥中。為此,實用新型人通過對赤泥進行分級,發(fā)現(xiàn),其中粒徑≥1.0mm的赤泥中氧化鈣占總赤泥氧化鈣量的60%,<0.074mm的赤泥Al2O3占總赤泥Al2O3量的90%,絕大部分的Al2O3富集在<0.074mm的赤泥中。為此預(yù)先對赤泥進行篩分處理,可以將赤泥中的鋁和鈉進行集中減量,進而便于后續(xù)的單獨分離,降低處理難度,提高回收鋁和鈉的效率。S200:回收鋁鈉根據(jù)本實用新型的具體實施例,利用本混合裝置將粒徑≥1.0mm的第一赤泥、粒徑<0.074mm的第三赤泥和添加劑進行混合,以便得到混合物料;利用第一焙燒裝置將混合物料進行第一焙燒處理,以便得到焙燒產(chǎn)物;在浸出裝置中利用堿液對焙燒產(chǎn)物進行浸出處理,以便得到含有鋁酸鈉的浸出液和浸出渣。由此,通過焙燒、浸出的方法可以有效地回收赤泥中的鋁和鈉。根據(jù)本實用新型的具體實施例,添加劑可以為碳酸鈉和氧化鈣的混合物。由于粒徑≥1.0mm的赤泥中的氧化鈣占總赤泥氧化鈣量的60%,因此將粒徑≥1.0mm的第一赤泥與粒徑<0.074mm的第三赤泥進行混合處理,可以有效地利用赤泥中的大部分氧化鈣,進而可以節(jié)省添加劑的用量,降低成本。根據(jù)本實用新型的具體實施例,碳酸鈉和氧化鈣的混合物與<0.074mm的赤泥混合后進行焙燒,碳酸鈉與赤泥中的Al2O3生成可以溶于堿液的Na2O·Al2O3,氧化鈣與赤泥中的SiO2生成2CaO·SiO2,防止SiO2與Al2O3生產(chǎn)Al2O3·SiO2,影響最終鋁的溶出。由此,通過上述焙燒處理,可以使得赤泥中的Al2O3生成可以溶于堿液的Na2O·Al2O3,進而便于后續(xù)鋁的浸出回收。根據(jù)本實用新型的具體實施了,添加劑中碳酸鈉的加入量可以按Na/Al=1.2-1.6(摩爾比)計算,氧化鈣加入量可以按Ca/Si=2.0-3.0(摩爾比)計算。由此可以加入適量的添加劑,避免浪費。根據(jù)本實用新型的具體實施例,第一焙燒處理的溫度為800-1100攝氏度,時間為20-50分鐘。由此可以使得赤泥中的Al2O3與碳酸鈉充分反應(yīng),進而提高鋁的回收率。根據(jù)本實用新型的具體實施例,利用堿液對焙燒產(chǎn)物進行浸出處理,以便得到含有鋁酸鈉的浸出液和浸出渣。由此,通過堿液浸出,使得鋁和鈉進入到浸出液中,其余保留在浸出渣中。進一步地,可以從含有鋁酸鈉的浸出液中回收鋁。進而實現(xiàn)從赤泥中單獨回收鋁。根據(jù)本實用新型的具體實施例,對焙燒產(chǎn)物進行浸出處理采用的堿液中Na2Ok的濃度為10-20g/L,Na2OC的濃度為3-8g/L。由此可以進一步提高浸出效率,提高鋁回收率。S300:回收鐵根據(jù)本實用新型的具體實施例,在混合成型裝置中將回收鋁后的浸出渣與粒徑<1.0mm且≥0.074mm的第二赤泥和還原劑進行混合成型處理,以便得到物料球團;以及利用第二焙燒裝置將物料球團進行第二焙燒處理,以便得到金屬化球團。根據(jù)本實用新型的具體實施例,第二焙燒處理的溫度為1200-1350攝氏度,時間為20-40分鐘。由此可以進一步提高焙燒效率,提高金屬鐵回收率。由此,將回收鋁后的浸出渣與含鋁量較少的粒徑<1.0mm且≥0.074mm的第二赤泥共同進行提鐵處理,可一步實現(xiàn)赤泥中金屬鐵的回收。由于預(yù)先對堿金屬進行單獨回收,不但可以提高混合赤泥的鐵品位和鐵的回收率,同時還可以減輕堿金屬對提鐵設(shè)備耐火材料的侵蝕。因此,本實用新型上述實施例的處理赤泥的方法可以高效回收赤泥中的鋁、鈉和鐵,達到對赤泥中的有價金屬進行分步高效回收利用。根據(jù)本實用新型的具體實施例,進一步可以采用熔分處理或者磨礦磁選處理,從金屬化球團中回收鐵。實施例1某冶煉赤泥,其成分為:Fe2O330.58%,Na2O6.26%,Al2O318.16%,SiO221.75%,CaO4.17%。經(jīng)過分級處理,得到粒度分別為≥1.0mm、<1.0mm且≥0.074mm和<0.074mm三種粒徑的赤泥。三種赤泥的成分及百分比見下表。粒度百分比Fe2O3Al2O3SiO2CaONa2O≥1.0mm6.223.511.516.1840.630.790.074mm~1.0mm21.0941.4915.4540.781.421.98<0.074mm72.6929.7320.3717.562.117.97將≥1.0mm和<0.074mm兩種粒徑赤泥混合,添加碳酸鈉和氧化鈣,碳酸鈉加入量按Na/Al=1.5(摩爾比)加入,氧化鈣加入量按Ca/Si=2.4(摩爾比)加入。將赤泥與添加劑混合均勻后焙燒,焙燒溫度為800℃,焙燒時間為40min。焙燒孰料用堿液溶出得到鋁酸鈉溶液和溶渣,鋁酸鈉溶液回收鋁。堿液Na2Ok濃度為15g/L,Na2OC濃度為5g/L。鋁回收率為87.32%,鈉回收率為78.39%。將溶出的溶渣與0.074mm~1.0mm的赤泥進行混合,添加25%的還原煤進行成型處理,得到的球團進行焙燒,焙燒溫度1250℃,焙燒時間30min。焙燒后得到鐵還原后的金屬化球團,金屬化球團通過熔分工藝回收鐵,鐵回收率為94.15%。實施例2某冶煉赤泥,其成分為:Fe2O330.58%,Na2O6.26%,Al2O318.16%,SiO221.75%,CaO4.17%。經(jīng)過分級處理,得到粒度分別為≥1.0mm、<1.0mm且≥0.074mm和<0.074mm三種粒徑的赤泥。三種赤泥的成分及百分比見下表。粒度百分比Fe2O3Al2O3SiO2CaONa2O≥1.0mm6.223.511.516.1840.630.790.074mm~1.0mm21.0941.4915.4540.781.421.98<0.074mm72.6929.7320.3717.562.117.97將≥1.0mm和<0.074mm兩種粒徑赤泥混合,添加碳酸鈉和氧化鈣,碳酸鈉加入量按Na/Al=1.2(摩爾比)加入,氧化鈣加入量按Ca/Si=2.0(摩爾比)加入。將赤泥與添加劑混合均勻后焙燒,焙燒溫度為1100℃,焙燒時間為25min。焙燒孰料用堿液溶出得到鋁酸鈉溶液和溶渣,鋁酸鈉溶液回收鋁。堿液Na2Ok濃度為20g/L,Na2OC濃度為7g/L。鋁回收率為86.78%,鈉回收率為80.13%。將溶出的溶渣與0.074mm~1.0mm的赤泥進行混合,添加20%的還原煤進行成型處理,得到的球團進行焙燒,焙燒溫度1250℃,焙燒時間30min。焙燒后得到鐵還原后的金屬化球團,金屬化球團通過磨礦磁選工藝回收鐵,鐵回收率為90.91%。在本說明書的描述中,參考術(shù)語“一個實施例”、“一些實施例”、“示例”、“具體示例”、或“一些示例”等的描述意指結(jié)合該實施例或示例描述的具體特征、結(jié)構(gòu)、材料或者特點包含于本實用新型的至少一個實施例或示例中。在本說明書中,對上述術(shù)語的示意性表述不必針對的是相同的實施例或示例。而且,描述的具體特征、結(jié)構(gòu)、材料或者特點可以在任一個或多個實施例或示例中以合適的方式結(jié)合。此外,在不相互矛盾的情況下,本領(lǐng)域的技術(shù)人員可以將本說明書中描述的不同實施例或示例以及不同實施例或示例的特征進行結(jié)合和組合。盡管上面已經(jīng)示出和描述了本實用新型的實施例,可以理解的是,上述實施例是示例性的,不能理解為對本實用新型的限制,本領(lǐng)域的普通技術(shù)人員在本實用新型的范圍內(nèi)可以對上述實施例進行變化、修改、替換和變型。當前第1頁1 2 3